CometNut
Aerospace
- Nov 8, 2022
- 9
thread2-491869
Hello, new to this forum. The above discussion was Closed, so I'm starting a new discussion.
I think there were some misstatements in the other discussion. The Comet 1 had a fuselage diameter of 10' 3", and the general skin thickness was 0.040". I forget what alloy was used, but it was of a more-brittle nature.
DeHavilland had several punch-riveting processes, but attached is a photo of an Erco punch-riveting machine used by DeHavilland for the Comet 1. In this photo, three 22' 0" x 2' 6" panels are being double-row-riveted to form a lap joint. The Erco machine had manual and automatic pitch movement controls, enabling the operator to move the pitch to the next riveting location. I believe it punched the holes, dimpled them, and then riveted them.
Hello, new to this forum. The above discussion was Closed, so I'm starting a new discussion.
I think there were some misstatements in the other discussion. The Comet 1 had a fuselage diameter of 10' 3", and the general skin thickness was 0.040". I forget what alloy was used, but it was of a more-brittle nature.
DeHavilland had several punch-riveting processes, but attached is a photo of an Erco punch-riveting machine used by DeHavilland for the Comet 1. In this photo, three 22' 0" x 2' 6" panels are being double-row-riveted to form a lap joint. The Erco machine had manual and automatic pitch movement controls, enabling the operator to move the pitch to the next riveting location. I believe it punched the holes, dimpled them, and then riveted them.
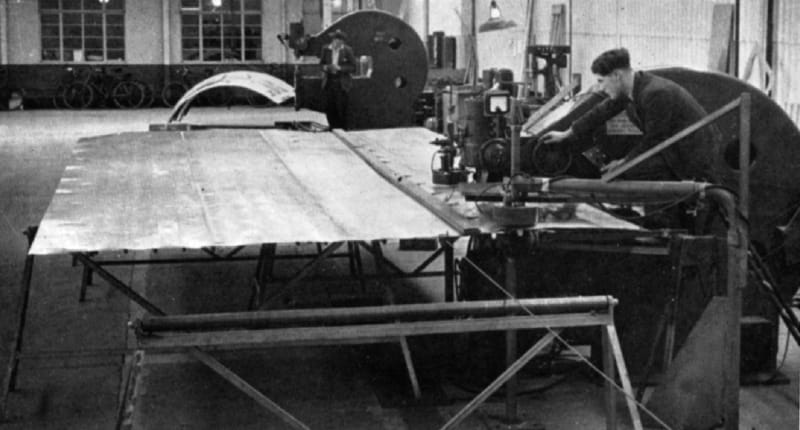