Hello fellow engineers, I need your help to verify if I can drill new holes on around the same PCD for this flange since the old holes are corroded and cannot be rethreaded, the operating pressure is about 35bars and the actual flange is only 160mm thick , the holes are about 55mm deep. Any software that I use to verify this?
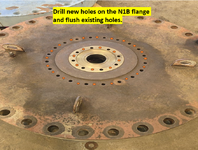
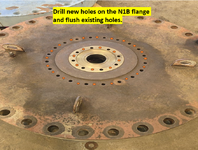
Last edited: