_Christos_
Mechanical
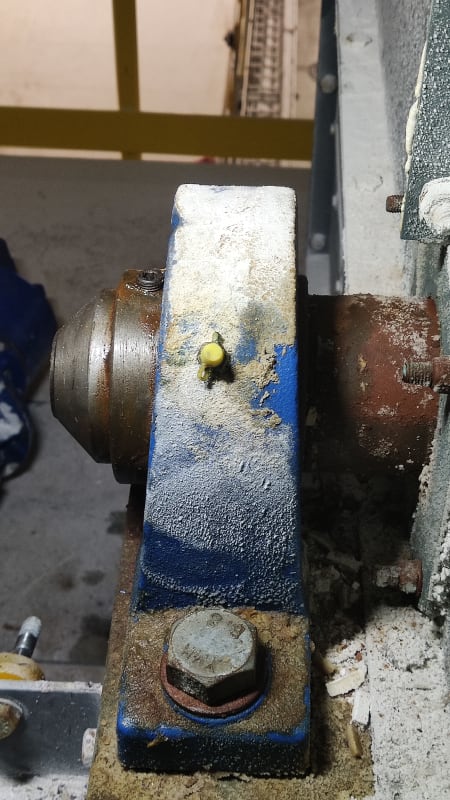
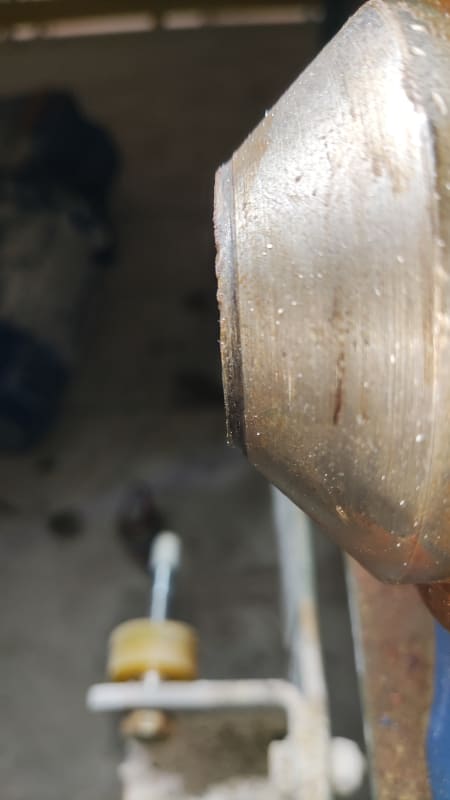
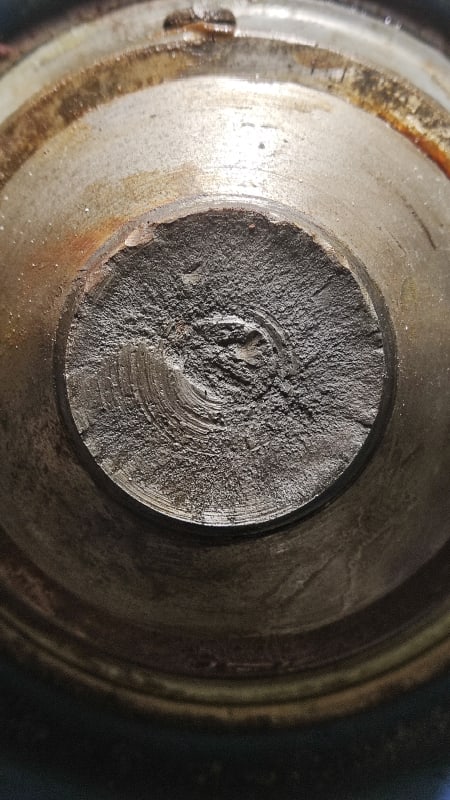
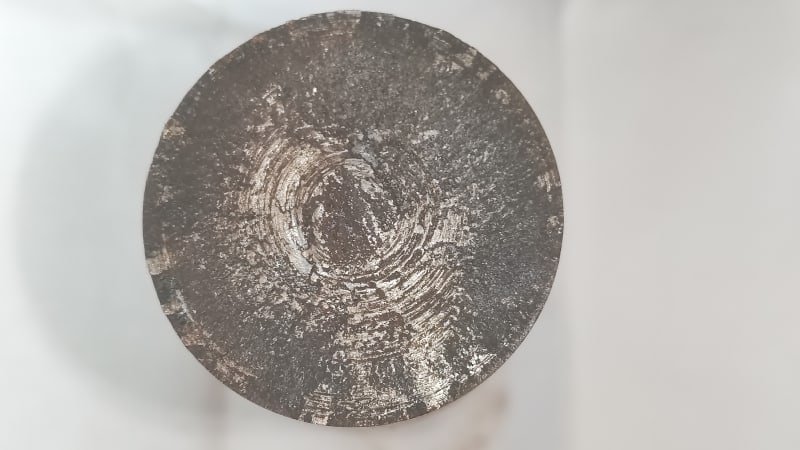
I hope everyone is well!
Can you help me diagnose the failure of this broken shaft?
This was on a bucket elevator, a gearmotor drove the wheel of the elevator through this shaft.
My preliminary findings suggest that this failed due to bending fatigue because the weight of the gearmotor was not adequately supported on the body of the elevator.
Can someone confirm this diagnosis or point me in the right direction?
I have attached photos of both sides of the break and of the broken off shaft on the machine before we took it out.
Thank you for reading!
Edit: I hope the attached images are visible now.