Greenalleycat
Structural
We do a lot of houses that use a ring-and-pile foundation i.e., concrete perimeter and internal timber piles
The perimeter is typically a 300mm wide trench and that has no polythene in it
We increase steel side cover from 50mm to 75mm for pouring against dirt and away we go
Yesterday I was on site and the contractor was insisting that there would be polythene in the trench
I'm 99% sure this was just because I was telling him to cut a bunch of roots back out of the trench and he wanted to be lazy and use polythene to keep them out instead
But I thought I'd go to the crowd and see if there is anything I'm missing
What do you lot do?
Edit: just to be clear, this is NOT for slab foundations. These always have DPM.
This discussion is ONLY for foundations of ring and pile type construction - see example below
The perimeter is typically a 300mm wide trench and that has no polythene in it
We increase steel side cover from 50mm to 75mm for pouring against dirt and away we go
Yesterday I was on site and the contractor was insisting that there would be polythene in the trench
I'm 99% sure this was just because I was telling him to cut a bunch of roots back out of the trench and he wanted to be lazy and use polythene to keep them out instead
But I thought I'd go to the crowd and see if there is anything I'm missing
What do you lot do?
Edit: just to be clear, this is NOT for slab foundations. These always have DPM.
This discussion is ONLY for foundations of ring and pile type construction - see example below
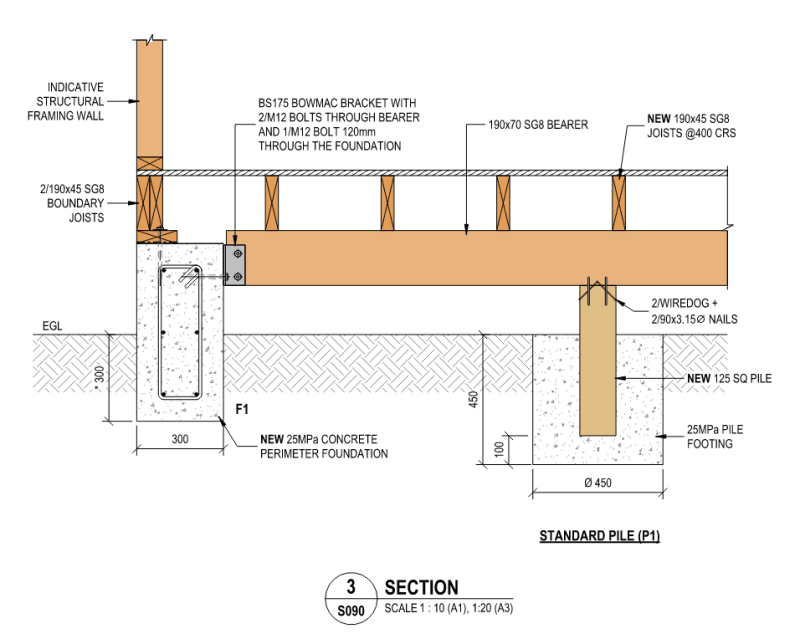