Hell Dear Engineers,
We have a vertical inline pump here that failed probably because of rotor unbalance.
Based on impeller sizes (Impeller OD:13.75” and width 0.5”), D/ B=27.5 since it is greater than 6, it should be static balance (which we did during previous repair about a year ago).
The pump rotor lost its center position during operation and rubbed to throat bushing and wear rings (please see attached pictures). Would you suggest dynamic balance even if D/B is greater than 6?
EDIT:
I wanted to add some more details to this post. Per API 610, impeller can be static balanced if D/B is greater than 6 and it can be dynamic balanced if D/B is less than 6. Where D is impeller diameter and B is shroud width of impeller at impeller OD.
Have you experienced a case where an impeller (for vertical inline pump) was static balanced but it was supposed to be dynamic balanced? What kind of damage was found on impeller? Thanks for reading.
Pump assembly drawing.
We have a vertical inline pump here that failed probably because of rotor unbalance.
Based on impeller sizes (Impeller OD:13.75” and width 0.5”), D/ B=27.5 since it is greater than 6, it should be static balance (which we did during previous repair about a year ago).
The pump rotor lost its center position during operation and rubbed to throat bushing and wear rings (please see attached pictures). Would you suggest dynamic balance even if D/B is greater than 6?
EDIT:
I wanted to add some more details to this post. Per API 610, impeller can be static balanced if D/B is greater than 6 and it can be dynamic balanced if D/B is less than 6. Where D is impeller diameter and B is shroud width of impeller at impeller OD.
Have you experienced a case where an impeller (for vertical inline pump) was static balanced but it was supposed to be dynamic balanced? What kind of damage was found on impeller? Thanks for reading.
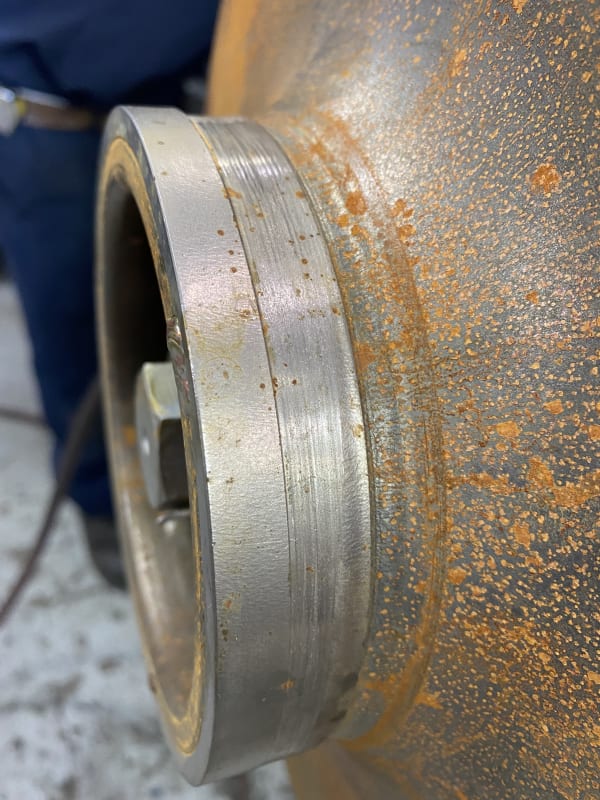
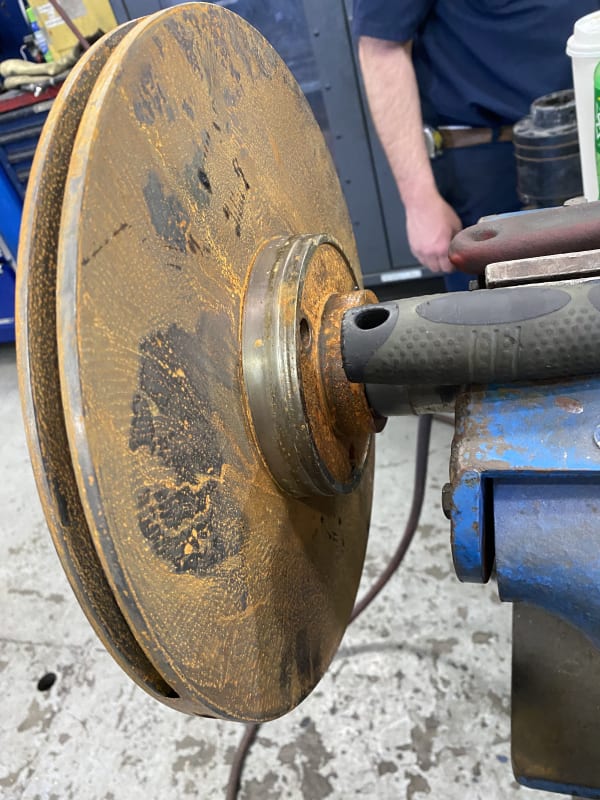
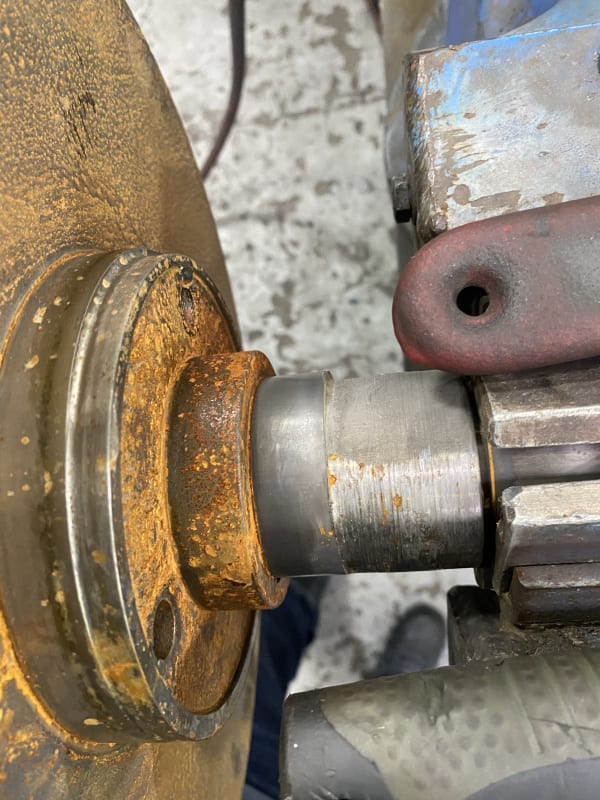
Pump assembly drawing.
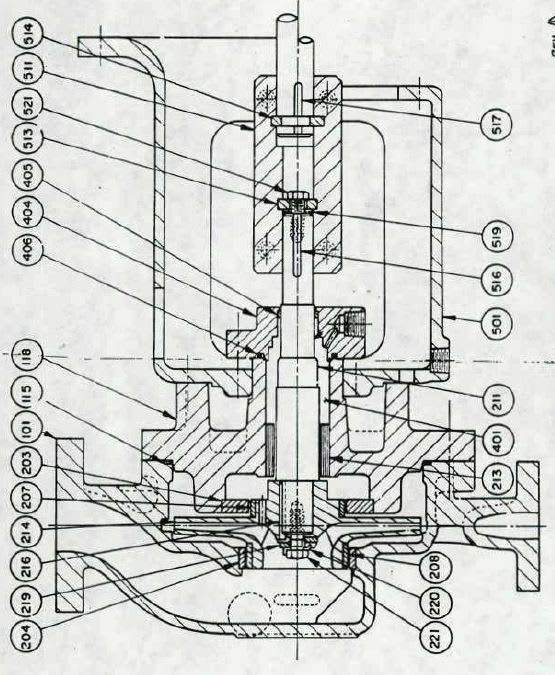