Hi guys,
Please see attached drawing from our customer.
The drawing attached only gives me Datum A and Datum B .
As you can see there are a lot of features to locate and orientate to.
The functionality of the component is Datum B goes against the mating part , with the shaded holes on the right hand side all being dowel hole which locate and orientate that part to the mating component .
Looking at the print and knowing how the part goes against the mating the component .
Could anyone suggest how to best change the drawing to have the correct features as a datum and correctly constrain all 6 degrees of freedom.
Thanks
R
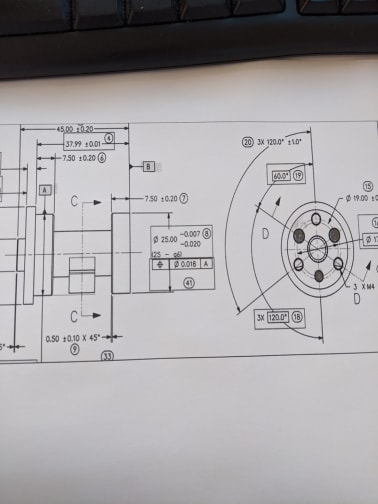
Please see attached drawing from our customer.
The drawing attached only gives me Datum A and Datum B .
As you can see there are a lot of features to locate and orientate to.
The functionality of the component is Datum B goes against the mating part , with the shaded holes on the right hand side all being dowel hole which locate and orientate that part to the mating component .
Looking at the print and knowing how the part goes against the mating the component .
Could anyone suggest how to best change the drawing to have the correct features as a datum and correctly constrain all 6 degrees of freedom.
Thanks
R