Anthony_J
Mechanical
- Aug 28, 2024
- 9
Hello,
I am working on designing a ventilation system for a 55-gallon drum. The goal is to remove as much contaminated airborne material from this drum as possible. My question is how to determine the point of diminishing returns on the throat opening to the vent device. I currently opened it from 1.25" opening to a 3.75" opening figuring I'd sacrifice some air velocity for more surface area. I don't have fluid flow software to model this so anyone with practical knowledge would be greatly appreciated. The air scrubber provides up to 750CFM.
Does anyone have any input/experience with this?
Thanks,
~Anthony
I am working on designing a ventilation system for a 55-gallon drum. The goal is to remove as much contaminated airborne material from this drum as possible. My question is how to determine the point of diminishing returns on the throat opening to the vent device. I currently opened it from 1.25" opening to a 3.75" opening figuring I'd sacrifice some air velocity for more surface area. I don't have fluid flow software to model this so anyone with practical knowledge would be greatly appreciated. The air scrubber provides up to 750CFM.
Does anyone have any input/experience with this?
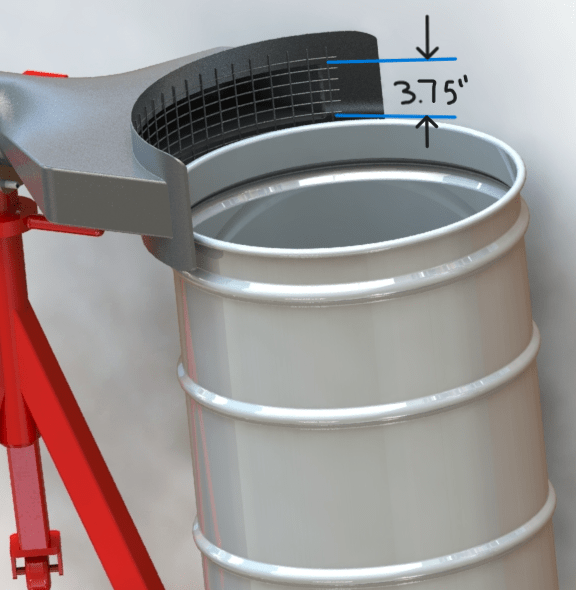
Thanks,
~Anthony