This is a project submittal for the variable chilled water pump, and I've noticed a suggestion from the consultant to include a balancing valve (DRV-double regulating type) alongside a butterfly isolation valve (BV). My concern lies in the following points:
The DRV concept seems to conflict with the variable flow concept, potentially resulting in unnecessary energy loss.
If the DRV is solely for isolation purposes, it raises the question of the necessity of the BV.
I would greatly appreciate your further insights and comments on this matter. Thank you.
The problem with the world is that intelligent people are full of doubts, while stupid ones are full of confidence.
-Charles Bukowski-
The DRV concept seems to conflict with the variable flow concept, potentially resulting in unnecessary energy loss.
If the DRV is solely for isolation purposes, it raises the question of the necessity of the BV.
I would greatly appreciate your further insights and comments on this matter. Thank you.
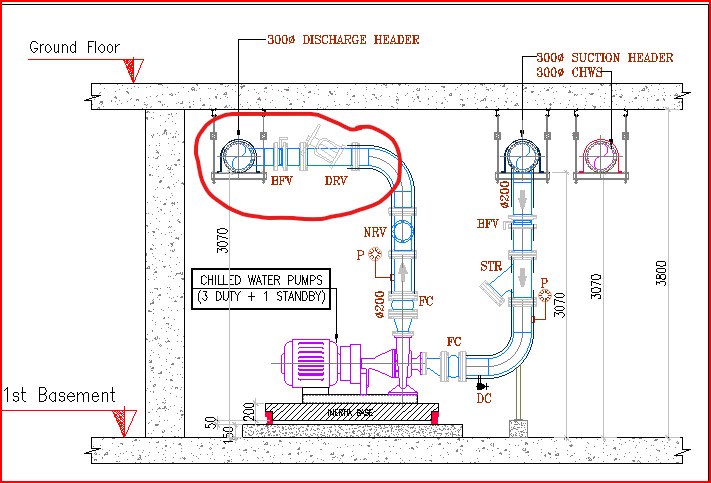
The problem with the world is that intelligent people are full of doubts, while stupid ones are full of confidence.
-Charles Bukowski-