Hello all,
I am trying to achieve the shape of the image below. I've been able to create a U bend but I am running into problems when trying to add the 150 deg bend, and maintaining the center of each tube end on the same plane. Any advice would be appreciate.
Best,
Canos
I am trying to achieve the shape of the image below. I've been able to create a U bend but I am running into problems when trying to add the 150 deg bend, and maintaining the center of each tube end on the same plane. Any advice would be appreciate.
Best,
Canos
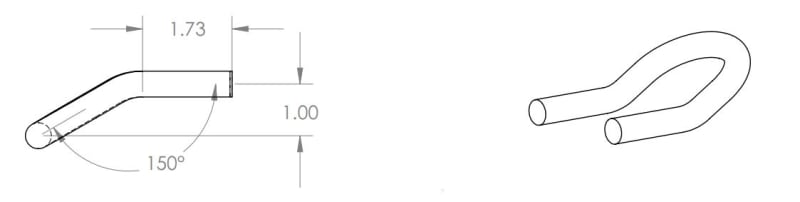