demedeirosa
Electrical
- Jun 23, 2012
- 15
I'm trying to decrease the amount of time it takes for an electromagnet to actuate. Currently we're driving it with two MOSFET's, to drop out both sides of the magnet. The MOSFET's im using are 300V, N-CH, link below. I am familiar with the idea of letting the inductive spike peak to decrease coil drop-out times, hence the reason for going with 300V MOSFET's with a 12V magnet. I was hoping that the 300V MOSFET would not clamp, therefore allowing my spike to quickly dissipate, but in reality I am clamping at roughly 16V.
Any one have any insight?
Any one have any insight?
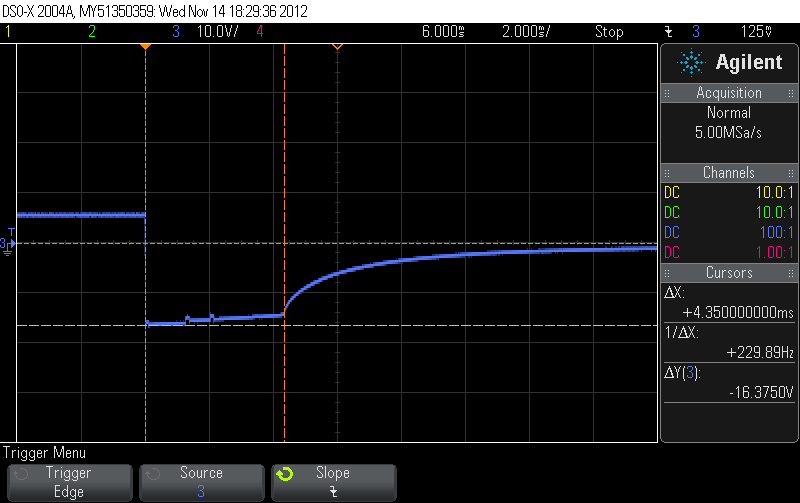