allimuthug
Civil/Environmental
- Oct 5, 2014
- 142
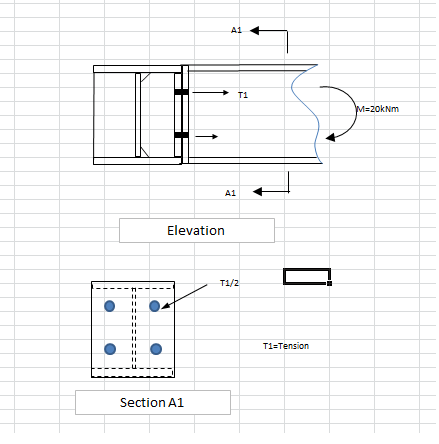
Hi
I have an End Plate Moment Connection, where there is tension in the End plate T1 From the Structural bolt.
Can anybody help me to calculate the thickness of the end plate due to tension of anchor bolt.