Hello,
I am looking for some information and thought of posting it here.
I have looked at various sites on sound, sound propagation, and sound attenuation but don’t seem to be able to find the answer I need.
I need to determine whether the sound will be damped better/easier/quicker through air vs. metal.
Intuitively, since air is easier to push around, it seems that it would dissipate the energy quicker/better than metal.
The 2nd part of my question is;
having a large quantity of tiny strands of metal in a wire with many small air spaces around them
vs. the same amount of metal and air space but with larger strands and large air spaces around the strands.
(Working with an engineer, he determined that there is essentially the same amount of air in both spaces)
Is the energy damped quicker by the tiny strands and air spaces, or is the attenuation the same in both cases?
If this type of information is shown or can be calculated on a site, please point me to it.
Thanks for any tips, pointers, or advice.
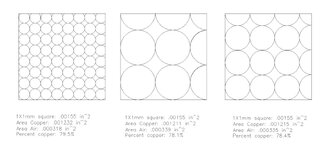
I am looking for some information and thought of posting it here.
I have looked at various sites on sound, sound propagation, and sound attenuation but don’t seem to be able to find the answer I need.
I need to determine whether the sound will be damped better/easier/quicker through air vs. metal.
Intuitively, since air is easier to push around, it seems that it would dissipate the energy quicker/better than metal.
The 2nd part of my question is;
having a large quantity of tiny strands of metal in a wire with many small air spaces around them
vs. the same amount of metal and air space but with larger strands and large air spaces around the strands.
(Working with an engineer, he determined that there is essentially the same amount of air in both spaces)
Is the energy damped quicker by the tiny strands and air spaces, or is the attenuation the same in both cases?
If this type of information is shown or can be calculated on a site, please point me to it.
Thanks for any tips, pointers, or advice.
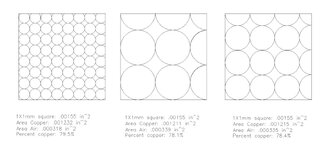