-
1
- #1
Dear all members,
I would like to invite all members to participate in this forum regarding discussion on defining minimum distance between welds. I know this questions has been asked many times in the past and answered but not with the exact technical explanation. I am a Researcher and will be conducting a experimental study on the topic but would like to consult all the practical engineers, inspectors, fabricators, contractors, clients, consultants out there before making a plan for this study. So i would like to ask some questions from all members and would like to review some initial study I have made till date.
Why proximity distance is maintained between welds Most international codes and specifications require a minimum distance (4T/5T/1D/1.5D) between two adjacent welds. Minimum distance is recommended to avoid adverse effect on the mechanical performance of the welded joint. e.g. fatigue and fracture of the weld-on-weld related to offshore structures. Possibility of altering the micro structure of existing weld and HAZ by application of the second weld. To avoid welding residual stress coupled with hardened micro structure in offshore environment.Regarding standards please find a review of minimum distance between welds in attached image.
In a typical Piping layout where 1000s of small piping / various pipe pups are welded with main line as per the compact layout and chances of welds coming closer are high.Various exemptions are provided by standards for near welds in case of branched connections like nozzles, tees etc without giving any technical justification. Radiography of joint is given as a testing excuse for such configurations by some standards. Fatigue in small piping is main concern due to vibrations and failure due to fatigue in close welds can be more catastrophic. In case of Repair procedure of replacing small pipe lengths there are high chances where welds in close proximity can arise without being able to maintain the minimum distance. No established WPS, PQR established for near welds configurations are established in case of repair where new welds comes closer to a existing weld which has been prone to fatigue, corrosion in his service life and hence a new weld close to a old one induces more residual stresses and susceptible micro structure between them.
Questions-1. How often does welds in close proximity is a non compliance to standards encountered in piping structures.
2. Can some of the members share any practical experiences with real time examples and pictures.
3. What is the practise adopted by all concerned at site to resolve this issue.
4. Any know failures occurred due to such configurations of welds.
5. During inspections how does asset management inspectors/ engineers perceive this problem.
6. Any other suggestions useful to conduct this study.
Thank you all in advance.
@thread378-215240, thread378-370184, thread292-257330, thread725-342321, thread378-242240
Regards
Sachin
I would like to invite all members to participate in this forum regarding discussion on defining minimum distance between welds. I know this questions has been asked many times in the past and answered but not with the exact technical explanation. I am a Researcher and will be conducting a experimental study on the topic but would like to consult all the practical engineers, inspectors, fabricators, contractors, clients, consultants out there before making a plan for this study. So i would like to ask some questions from all members and would like to review some initial study I have made till date.
Why proximity distance is maintained between welds Most international codes and specifications require a minimum distance (4T/5T/1D/1.5D) between two adjacent welds. Minimum distance is recommended to avoid adverse effect on the mechanical performance of the welded joint. e.g. fatigue and fracture of the weld-on-weld related to offshore structures. Possibility of altering the micro structure of existing weld and HAZ by application of the second weld. To avoid welding residual stress coupled with hardened micro structure in offshore environment.Regarding standards please find a review of minimum distance between welds in attached image.
In a typical Piping layout where 1000s of small piping / various pipe pups are welded with main line as per the compact layout and chances of welds coming closer are high.Various exemptions are provided by standards for near welds in case of branched connections like nozzles, tees etc without giving any technical justification. Radiography of joint is given as a testing excuse for such configurations by some standards. Fatigue in small piping is main concern due to vibrations and failure due to fatigue in close welds can be more catastrophic. In case of Repair procedure of replacing small pipe lengths there are high chances where welds in close proximity can arise without being able to maintain the minimum distance. No established WPS, PQR established for near welds configurations are established in case of repair where new welds comes closer to a existing weld which has been prone to fatigue, corrosion in his service life and hence a new weld close to a old one induces more residual stresses and susceptible micro structure between them.
Questions-1. How often does welds in close proximity is a non compliance to standards encountered in piping structures.
2. Can some of the members share any practical experiences with real time examples and pictures.
3. What is the practise adopted by all concerned at site to resolve this issue.
4. Any know failures occurred due to such configurations of welds.
5. During inspections how does asset management inspectors/ engineers perceive this problem.
6. Any other suggestions useful to conduct this study.
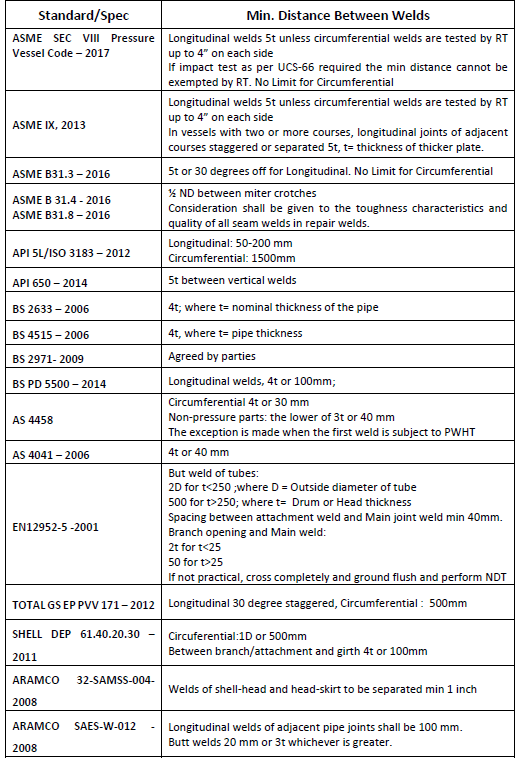
Thank you all in advance.
@thread378-215240, thread378-370184, thread292-257330, thread725-342321, thread378-242240
Regards
Sachin