hootrpootr
Aerospace
Hello,
I have a question I was hoping you all could answer. A coworker sent me an FE model that he created, where he modeled a bolted joint using just an RBE2 element (with DOFs in 123) to connect the matching holes in 2 plates. I would never do this; my preferred modeling method would be to add a CBUSH element between the two holes and then connect each end to their respective plate with an RBE2.
Is it even possible to extract usable MPC forces from my coworker's model? When I plot the MPC forces marker, I get 0 lbf in every direction. Is this due to the summation of forces at the independent node or something? I know that RBE2s are infinitely stiff, so I suspect any forces/stresses at this type of joint wouldn't even be realistic or worth assessing.
I've attached a picture of a quick FEA mockup of a joint with just an RBE2 vs my preferred method of a CBUSH w/ RBE2s.
Thanks for the input!
I have a question I was hoping you all could answer. A coworker sent me an FE model that he created, where he modeled a bolted joint using just an RBE2 element (with DOFs in 123) to connect the matching holes in 2 plates. I would never do this; my preferred modeling method would be to add a CBUSH element between the two holes and then connect each end to their respective plate with an RBE2.
Is it even possible to extract usable MPC forces from my coworker's model? When I plot the MPC forces marker, I get 0 lbf in every direction. Is this due to the summation of forces at the independent node or something? I know that RBE2s are infinitely stiff, so I suspect any forces/stresses at this type of joint wouldn't even be realistic or worth assessing.
I've attached a picture of a quick FEA mockup of a joint with just an RBE2 vs my preferred method of a CBUSH w/ RBE2s.
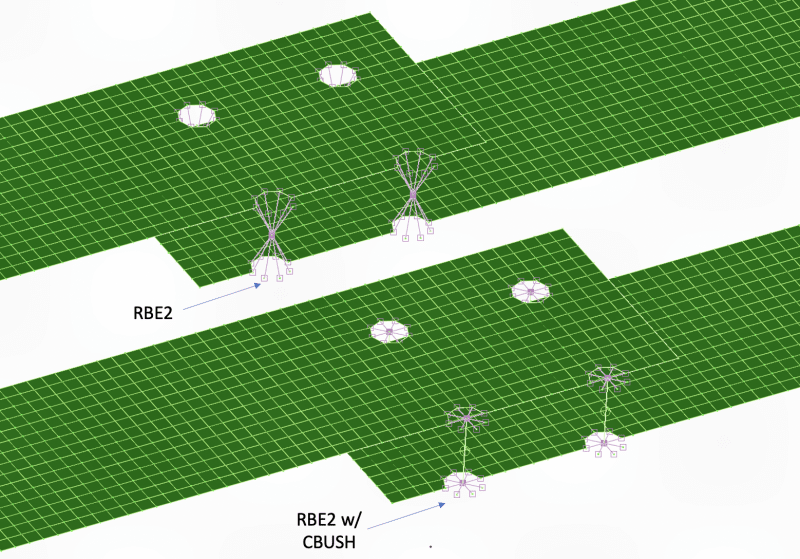
Thanks for the input!