Hey Everyone,
This is my first post over here. I need help with verification of FEA results. The simulation consists of a plate exposed to a uniform load on it. The tricky part is that the plate has a complex shape as shown in the photo.
How does one verify results for complex shapes? I tried hand calculations, assuming simple beam and plate, but the results showed a error of more than 45%.
Any advice would be appreciated.
This is my first post over here. I need help with verification of FEA results. The simulation consists of a plate exposed to a uniform load on it. The tricky part is that the plate has a complex shape as shown in the photo.
How does one verify results for complex shapes? I tried hand calculations, assuming simple beam and plate, but the results showed a error of more than 45%.
Any advice would be appreciated.
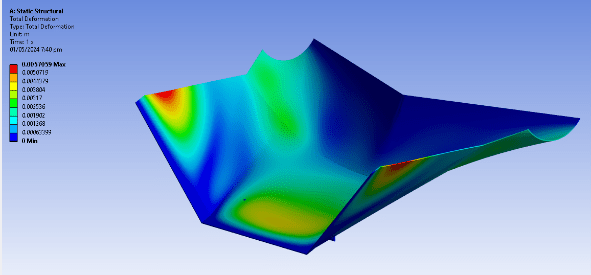