canadiancastor
Structural
I'm trying to understand an example in Bathe's Finite Element procedures, but there is something I'm missing. He goes from elements stress to equivalent nodal point forces (he says "in the virtual work sense"), but I don't understand he's doing the transition. Can the forces at element nodal points be fully determined by the element stress only, and can I do it simply by hand?
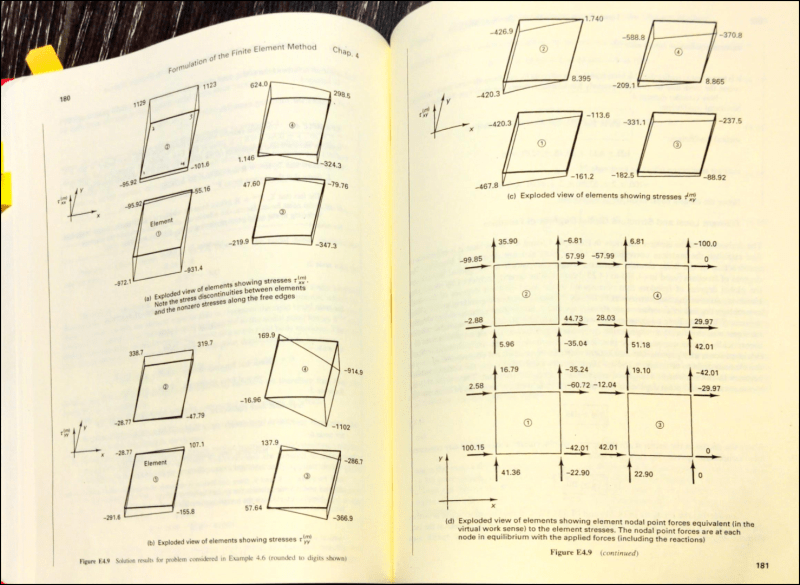