Backcheckrage
Structural
- Sep 23, 2012
- 84
I'm working in AUS/NZ. I've got these tension-compression rods which are supporting precast cladding panels under faceload. The issue is that I need these things to be good for 60minute fire rating. How can that be checked? I tried to use formulas in NZS3404 section 11.6 (snap below) -but I only get 15mins or so. Can these things be intumescent painted? Has anyone done this before?
the detail:
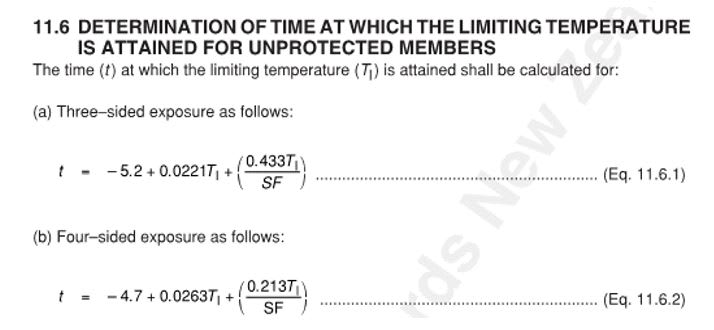
the detail:
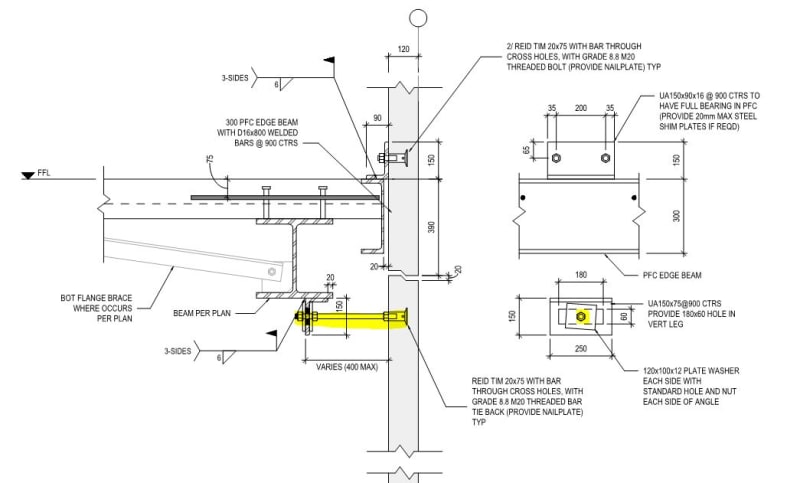