adrianstructures
Civil/Environmental
I have a question.. why do many engineers model the main mast connection as well as the other connections as being in the structural calculation model as pinned and not fixed?
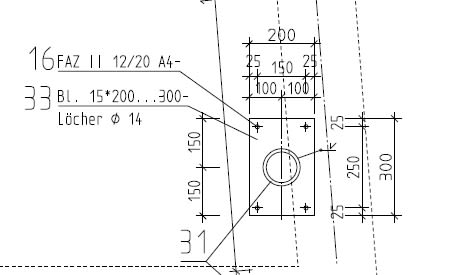
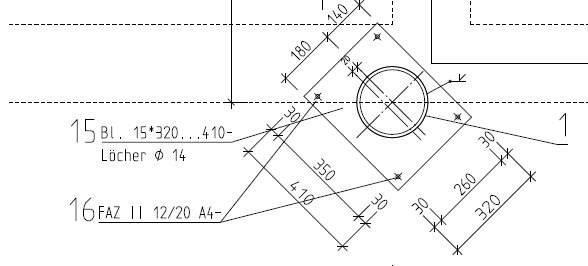
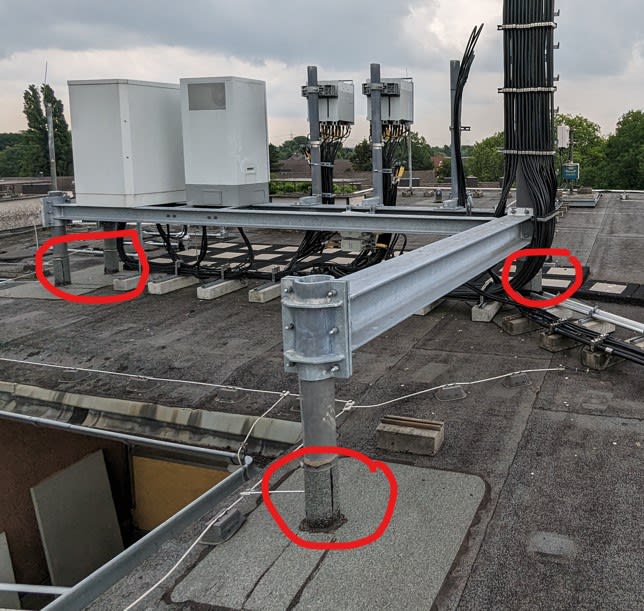
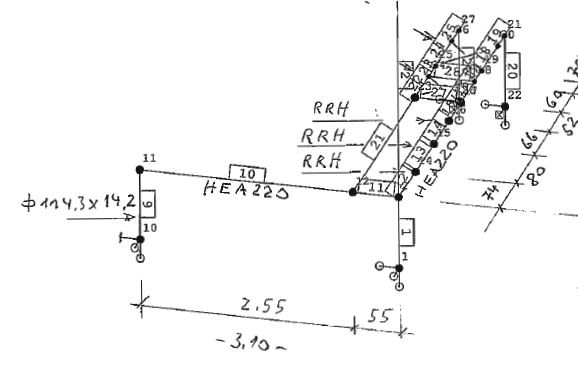
Follow along with the video below to see how to install our site as a web app on your home screen.
Note: This feature may not be available in some browsers.
phamENG said:Why do we do it? Because we don't want moment transferred down into the roof slab. If we assume that no moment is transferred, the resulting stiffness of the frame is high enough that very little moment gets transferred. Of course, some will get transferred and we have to be aware of that and design for it. But no model is ever 100% representative of reality. So we make up a plausible story, create a model around it, and then make sure the actual detailing makes room for what will really happen.
phamENG said:Now, can we talk about that extended end plate moment connection to the pipe column?
Then, it probably doesn't matter what you assume, unless you are in Dade County, FL. Otherwise, you are dealing with live load, and, in this particular case, roof live load, which will only occur when the roof is re-roofed or there is a fire.phamENG said:But I don't do seismic