adrianstructures
Civil/Environmental
I have a question.. why do many engineers model the main mast connection as well as the other connections as being in the structural calculation model as pinned and not fixed?
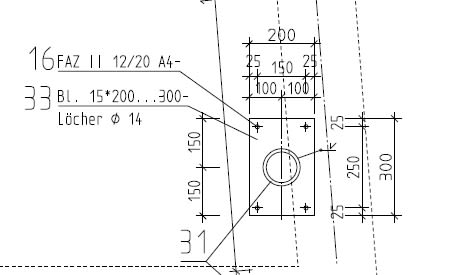
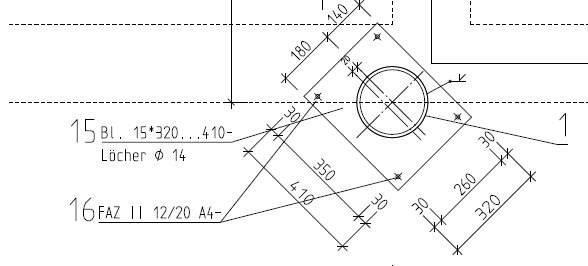
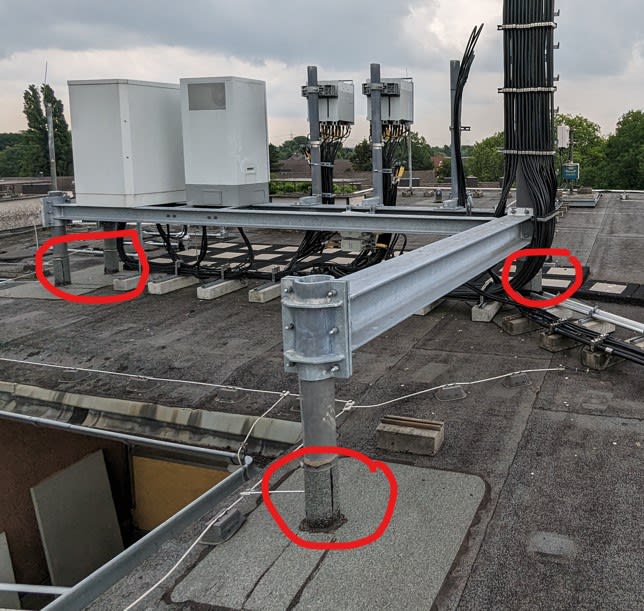
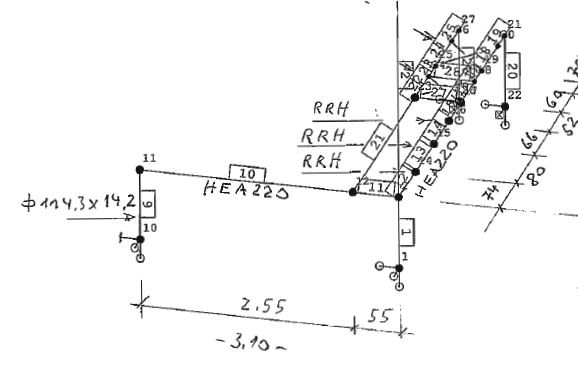
Follow along with the video below to see how to install our site as a web app on your home screen.
Note: This feature may not be available in some browsers.
This is the epitome of "calling a tail a leg" analogy. Just because you call it a pin to "force the moment connection" doesn't make it so.dik said:They can be fixed or pinned... I'd usually use pinned to force the moment connection
You don't "assign" moment at the base. Nature does that. Our modeling should represent nature, not to make up our own fairy tale.hokie66 said:What's it actually supported by? Before you assign a lot of moment at the base, you have to know how that will be developed. From the sketch, it looks like a few short pins connect it to a thin slab. If those drilled in anchors are going to pull out, it is foolish to depend on fixity. Too much modeling, too little common sense.
This is the closest comment to reality I've seen on this and similar topics. You are describing progressive collapse. Wonderful! How do you know that assumption is valid? If/when those anchors pull out, what happens then? Do you still have shear capacity? Uplift capacity?rb1957 said:The assumption is that the joint loses moment stiffness before it loses shear stiffness that a "fixed" joint will yield to a "pinned" joint and then fail.
as an example.phamENG said:It may only add an hour to the project...but they add up. While not as impactful to me running things solo, my last firm could have employed an extra engineer for the time it would take to do that on every project.
JStephen said:The original question was "why do many engineers model...as pinned and not fixed?", not "which is it, really".
phamENG said:So we make up a plausible story, create a model around it, and then make sure the actual detailing makes room for what will really happen.
What I have been thinking is fixed connection transfers moment to the base hence more conservative than a pinned connection which doesn't transfer moment. Can you please explain what am I missing?
rb1957 said:ok, take a joint fasteners,...
rb1957 said:He'll yield first and the moment stiffness will drop significantly.
rb1957 said:Sure, you can say (correctly) that it is an assumption, that the fasteners could unzip (fail progressively).
rb1957 said:But a tonne of experience is telling you that this "doesn't" happen, that many other things will fail before you need to consider the moment stiffness of a joint. But work it out for yourself, build your own experience so you don't rely on "heard it on the internet".
rb1957 said:build your own experience