Asisraja D
Mechanical
- Jan 3, 2024
- 192
Hi all
I have a doubt on flow rates for fire hydrant landing valves. we have selected 100 mm X 80 mm Oblique type single head landing valves for our plant and we get 63mm orifice diameter but as per vendor specification it shows testing flow rate around 900 liters per minute at 7 bar pressure but for my understanding how can we get that much flow rate at 63mm nozzle and it is possible only if we consider 4.8 m/s velocity for the hydrant flow but i am bit confusing here at what will be the use of pressure here at 7 bar when we achieve this much flow rate ? or this pressure may be conserved at the discharge side in terms of 900 lpm ? can anyone please explain me in this.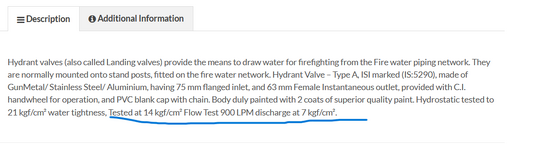
I have a doubt on flow rates for fire hydrant landing valves. we have selected 100 mm X 80 mm Oblique type single head landing valves for our plant and we get 63mm orifice diameter but as per vendor specification it shows testing flow rate around 900 liters per minute at 7 bar pressure but for my understanding how can we get that much flow rate at 63mm nozzle and it is possible only if we consider 4.8 m/s velocity for the hydrant flow but i am bit confusing here at what will be the use of pressure here at 7 bar when we achieve this much flow rate ? or this pressure may be conserved at the discharge side in terms of 900 lpm ? can anyone please explain me in this.
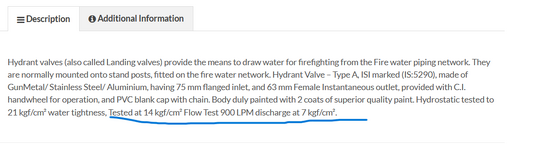