Logan82
Structural
- May 5, 2021
- 212
Hi!
I have seen several footbridges with this configuration:
I am wondering how such footbridge configuration are allowed considering that there are no diaphragms or bracings at the supports, like this:
Note that I am sure these are allowed considering that there are many footbridges like this. I am trying to figure out how to justify that through code or calculation.
To have diaphragms at the supports like what I have drawn, it implies that the footbridge deck is on top of the steel truss structure.
Diaphragms and bracings are required at the supports according to CSA S6.
This is a follow-up of this thread:
I have seen several footbridges with this configuration:
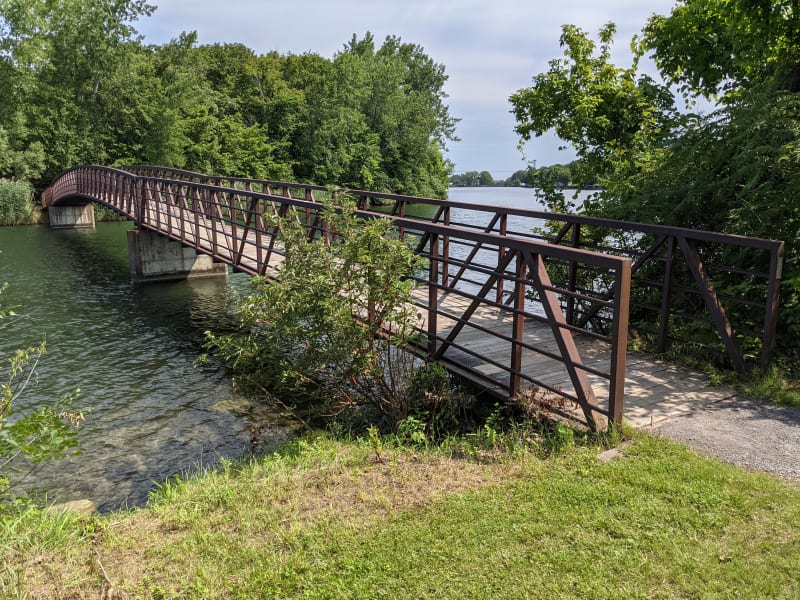
I am wondering how such footbridge configuration are allowed considering that there are no diaphragms or bracings at the supports, like this:
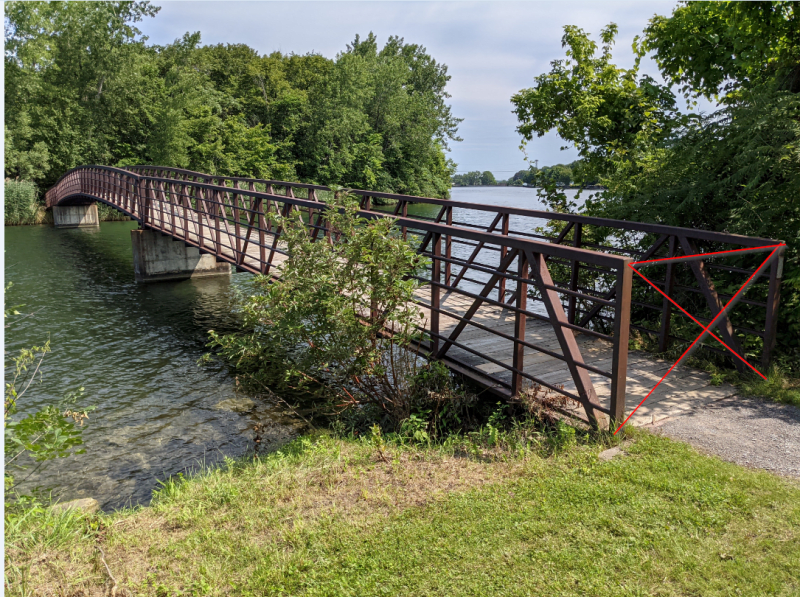
Note that I am sure these are allowed considering that there are many footbridges like this. I am trying to figure out how to justify that through code or calculation.
To have diaphragms at the supports like what I have drawn, it implies that the footbridge deck is on top of the steel truss structure.
Diaphragms and bracings are required at the supports according to CSA S6.

This is a follow-up of this thread: