gersen
Materials
- Nov 14, 2017
- 27
Hello, I'm struggling with a force problem.
I have a system where a mass P, connected to rod od variable length L. The mass is guided to move on the circumference 31500 mm.
To lift the mass I apply a force of 1700 KN on the same direction of the rod.
What I need to find is the force componet orthogonal to the rod (N), if there is.
Here the scheme:
Just for info this is a schematic rapresentation of a radial gate and I'm trying to find the bending stress on the rod, if there is any.
I have a system where a mass P, connected to rod od variable length L. The mass is guided to move on the circumference 31500 mm.
To lift the mass I apply a force of 1700 KN on the same direction of the rod.
What I need to find is the force componet orthogonal to the rod (N), if there is.
Here the scheme:
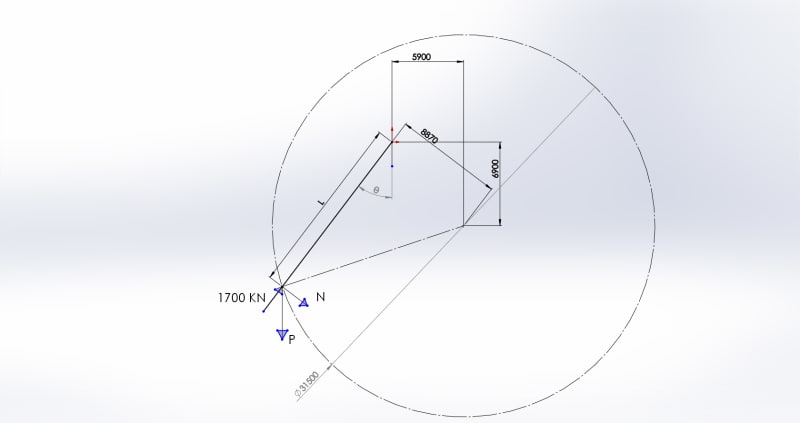
Just for info this is a schematic rapresentation of a radial gate and I'm trying to find the bending stress on the rod, if there is any.