Richard A
Mechanical
- Dec 11, 2018
- 4
Hello,
I stuck without an engineer for a couple of weeks and was hoping someone could point me in the right direction.
In the diagram below I need to determine the cylinder pressure required to move the "hinged body" from the closed position (on the right) to the open position (on the left).
Any help would be greatly appreciated.
I stuck without an engineer for a couple of weeks and was hoping someone could point me in the right direction.
In the diagram below I need to determine the cylinder pressure required to move the "hinged body" from the closed position (on the right) to the open position (on the left).
Any help would be greatly appreciated.
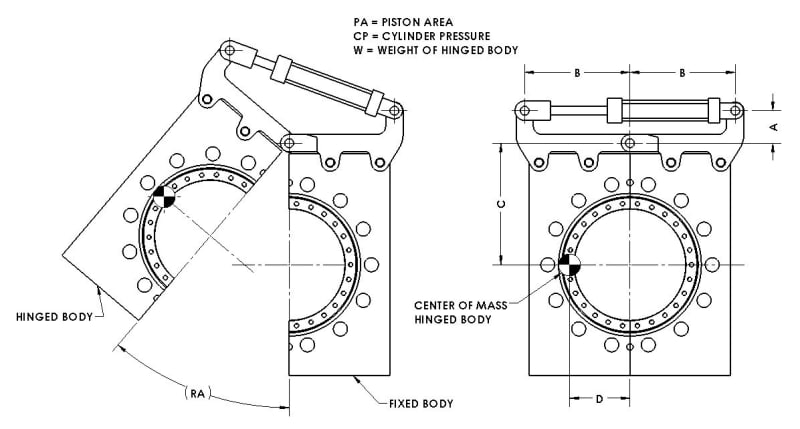