EK1989
Structural
- Jul 19, 2019
- 6
Hi,
I am trying to verify the section properties that my software provides me for the warping constant but I can not find out how the warping constant is calculated. I have a box section with width and height 2 in and thickness 0.5 in. The warping constant that the software gives me is equal to 0.00730 in^6. Does anyone know if there is an explicit formula to calculate the warping constant of a box section? Although, the warping effects may be negligible in these sections, I would like to check it with some hand calculations.
Thank you in advance!
Kind regards,
Emmanouil
I am trying to verify the section properties that my software provides me for the warping constant but I can not find out how the warping constant is calculated. I have a box section with width and height 2 in and thickness 0.5 in. The warping constant that the software gives me is equal to 0.00730 in^6. Does anyone know if there is an explicit formula to calculate the warping constant of a box section? Although, the warping effects may be negligible in these sections, I would like to check it with some hand calculations.
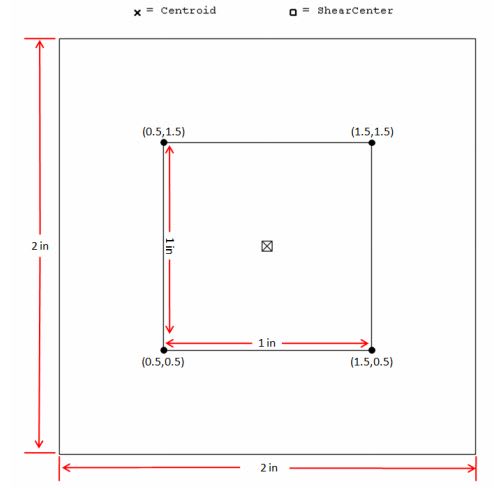
Thank you in advance!
Kind regards,
Emmanouil