Hello Everyone!
I have an application where I use a VFD to control a 3-Phase AC motor. The application involves a lift which is used to transfer a load from point A to B and after unloading the lift needs to return from Point B to A.
I currently am using two Normally-Open push buttons for Forward and Reverse movement and two Normally-Closed limit switches installed at point A and point B which when activated gives the STOP command to the VFD.
The twist is this:
1. After the FORWARD pushbutton is activated, the lift reaches point B and stops at the limit switch B. If the operator gives the Forward command AGAIN instead of Reverse command by mistake, then this would be disastrous since the lift will move forward beyond the limit switch and the lift cable will break.
Can anyone please suggest me a wiring method I can use to eliminate the above from happening? I hope I made myself clear with the above explanation. Please feel free to ask anything! Any help is greatly appreciated! I have also attached the simplified wiring diagram that I am currently using (SB2 refers to Normally Closed Limit Switch).
I have an application where I use a VFD to control a 3-Phase AC motor. The application involves a lift which is used to transfer a load from point A to B and after unloading the lift needs to return from Point B to A.
I currently am using two Normally-Open push buttons for Forward and Reverse movement and two Normally-Closed limit switches installed at point A and point B which when activated gives the STOP command to the VFD.
The twist is this:
1. After the FORWARD pushbutton is activated, the lift reaches point B and stops at the limit switch B. If the operator gives the Forward command AGAIN instead of Reverse command by mistake, then this would be disastrous since the lift will move forward beyond the limit switch and the lift cable will break.
Can anyone please suggest me a wiring method I can use to eliminate the above from happening? I hope I made myself clear with the above explanation. Please feel free to ask anything! Any help is greatly appreciated! I have also attached the simplified wiring diagram that I am currently using (SB2 refers to Normally Closed Limit Switch).
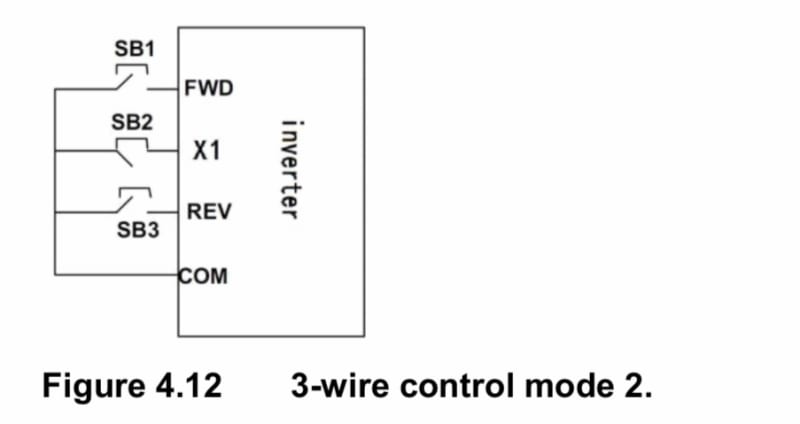