Paul Teggart
Structural
- Jul 21, 2023
- 3
Hi, first post on here so please bear with me if I am showing my ignorance this early.
I was wondering if someone could help me with their opinion on what may have happened here.
This rotating drum pulley was returned from our customer and the faces of the failure have got me scratching my head.
There is a heavy 50mm boss welded onto the face of the 12mm plate with a fillet weld, or at least the joint should be composed like, but we think there is a possibility it was assembled as in file name. I have attached these for you consideration, as well as the pictures to give you some perspective on the failure, and show the faces of the failure in detail. The "swirly" nature of the faces has confused me.
I am so grateful to anyone who considers this even if they have nothing to add, and if anyone has any more questions please do not hesitate to ask me.
Many thanks in advance.
I was wondering if someone could help me with their opinion on what may have happened here.
This rotating drum pulley was returned from our customer and the faces of the failure have got me scratching my head.
There is a heavy 50mm boss welded onto the face of the 12mm plate with a fillet weld, or at least the joint should be composed like, but we think there is a possibility it was assembled as in file name. I have attached these for you consideration, as well as the pictures to give you some perspective on the failure, and show the faces of the failure in detail. The "swirly" nature of the faces has confused me.
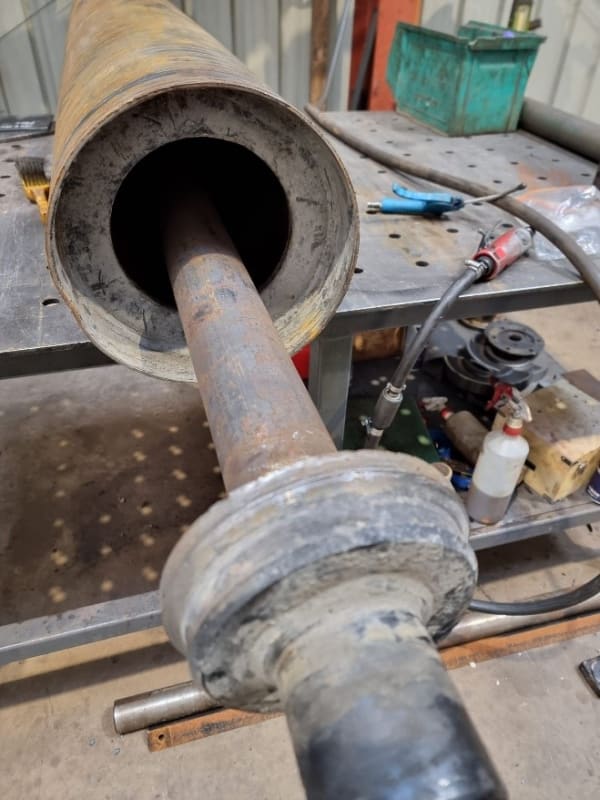
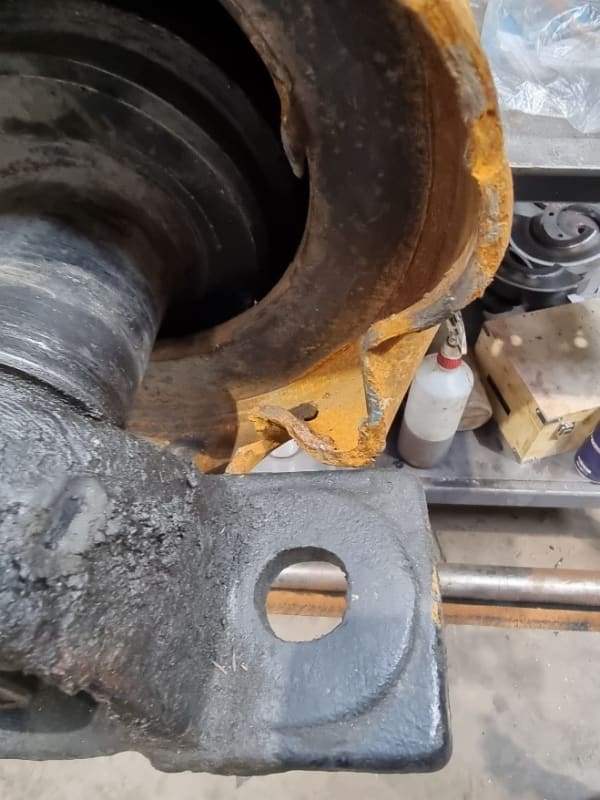
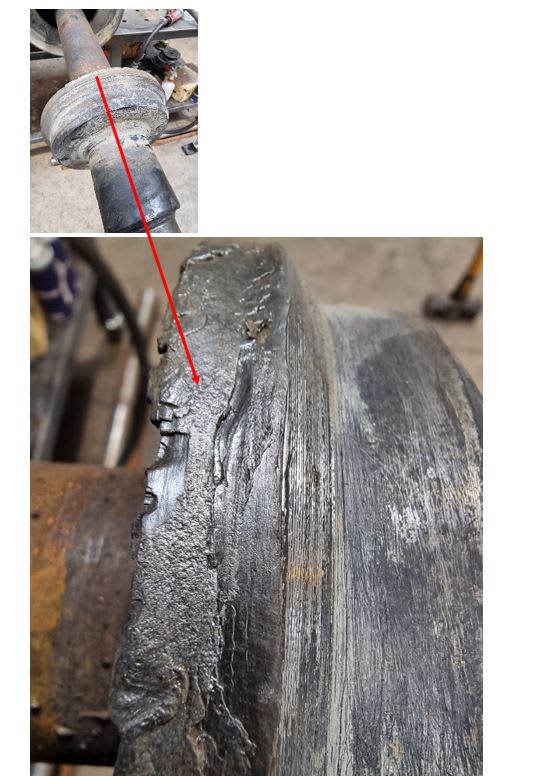
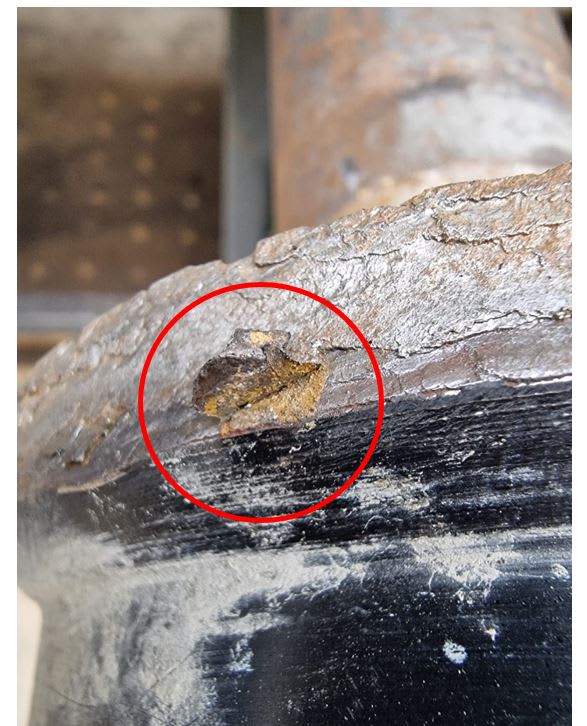
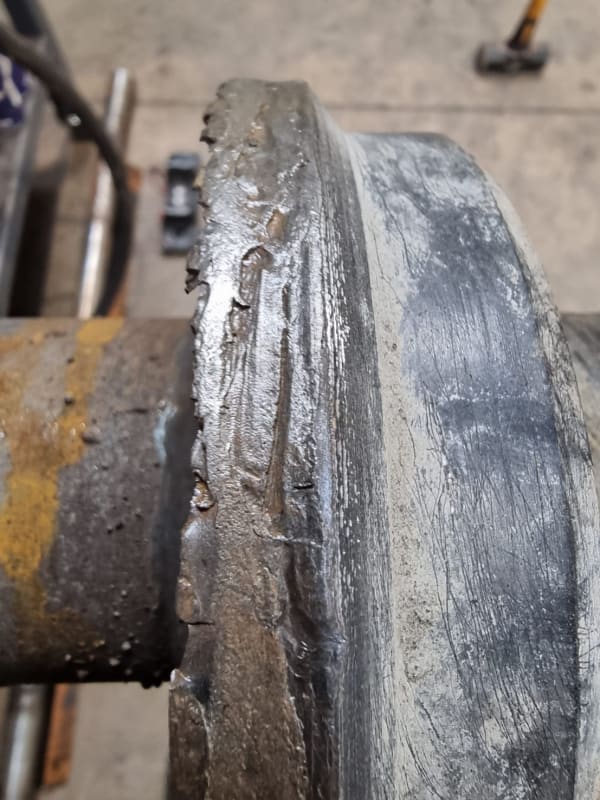
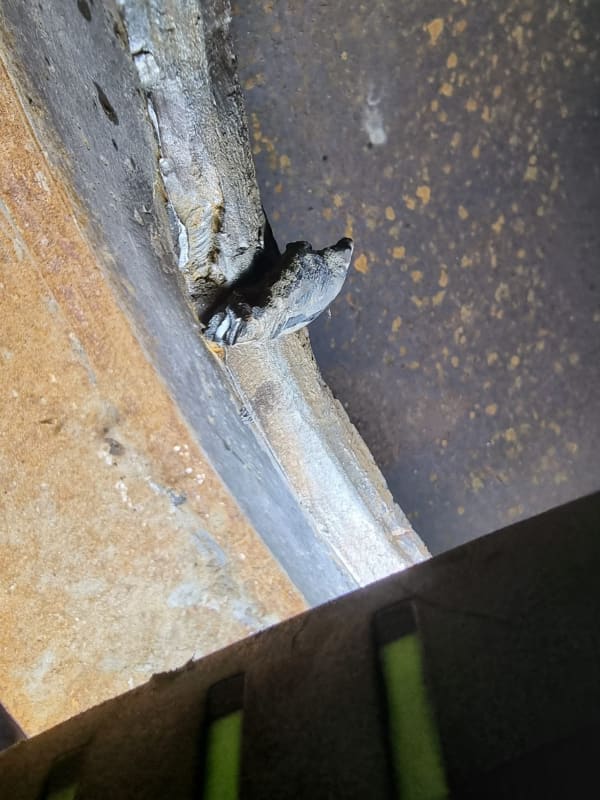
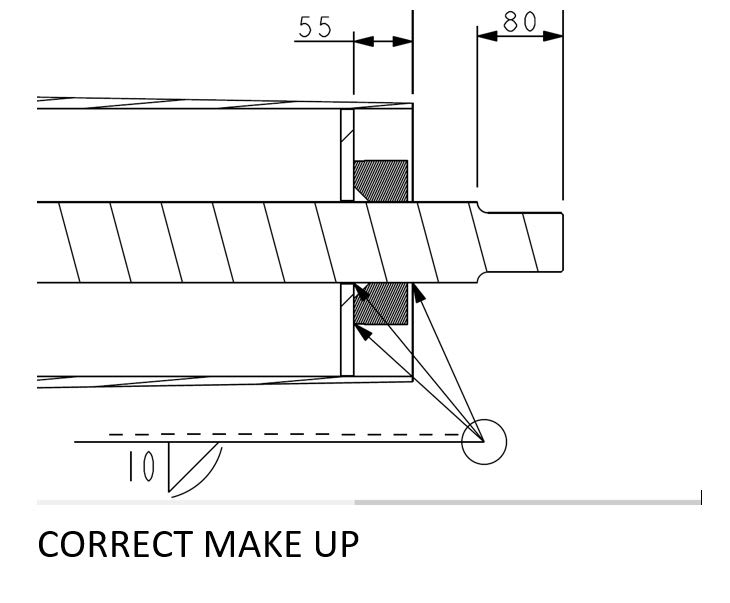
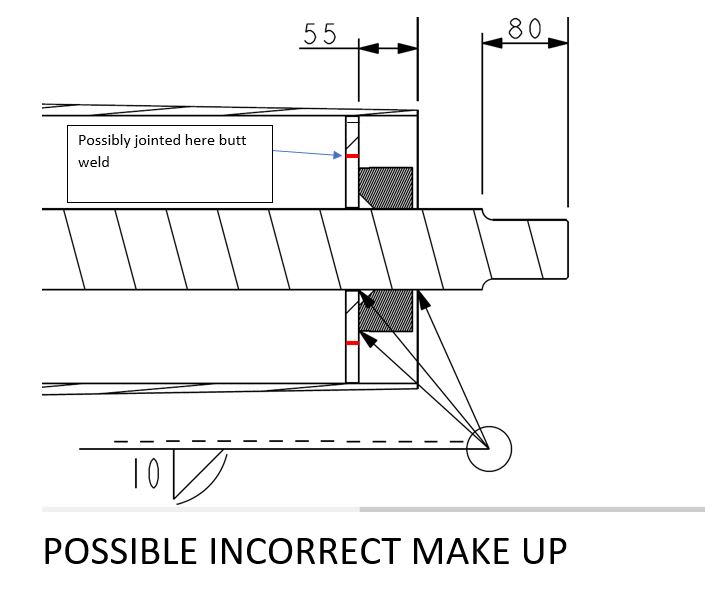
I am so grateful to anyone who considers this even if they have nothing to add, and if anyone has any more questions please do not hesitate to ask me.
Many thanks in advance.