-
1
- #1
Nashanas
Petroleum
- Apr 23, 2021
- 54
Hello everyone,
I have a very basic question about gear train design.
In this design, it can be seen that there is a set of 3 gears with same ratio, which are being used to move the bigger gear. I want to usa only one gear instead of three to move the bigger gear. But I have been told that 3 gears are used to reduce tooth stress. But according to Shigley, the delivered load from one gear tooth to another depends on the pitch, face width and material. If all these variables are same, I dont see any reason for using 3 gears instead of one, as the load delviered will remain the same.
I have a very basic question about gear train design.
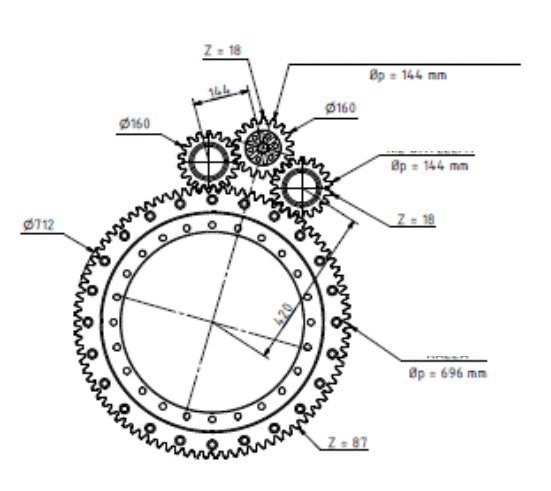
In this design, it can be seen that there is a set of 3 gears with same ratio, which are being used to move the bigger gear. I want to usa only one gear instead of three to move the bigger gear. But I have been told that 3 gears are used to reduce tooth stress. But according to Shigley, the delivered load from one gear tooth to another depends on the pitch, face width and material. If all these variables are same, I dont see any reason for using 3 gears instead of one, as the load delviered will remain the same.