Hello!
I am trying to join steel with methacrylate, I have tried a glue that adheres to different materials, like 3m DP8405, but the adhesion is very poor, I have tried to use an acrylic epoxy like Weld-on 42, I cover the whole screw, encapsulating in a single piece inside the methacrylate, are there more alternatives for gluing metal with acrylic?
Thank you!!!!!!!!!!!!!!!!!!!
I am trying to join steel with methacrylate, I have tried a glue that adheres to different materials, like 3m DP8405, but the adhesion is very poor, I have tried to use an acrylic epoxy like Weld-on 42, I cover the whole screw, encapsulating in a single piece inside the methacrylate, are there more alternatives for gluing metal with acrylic?
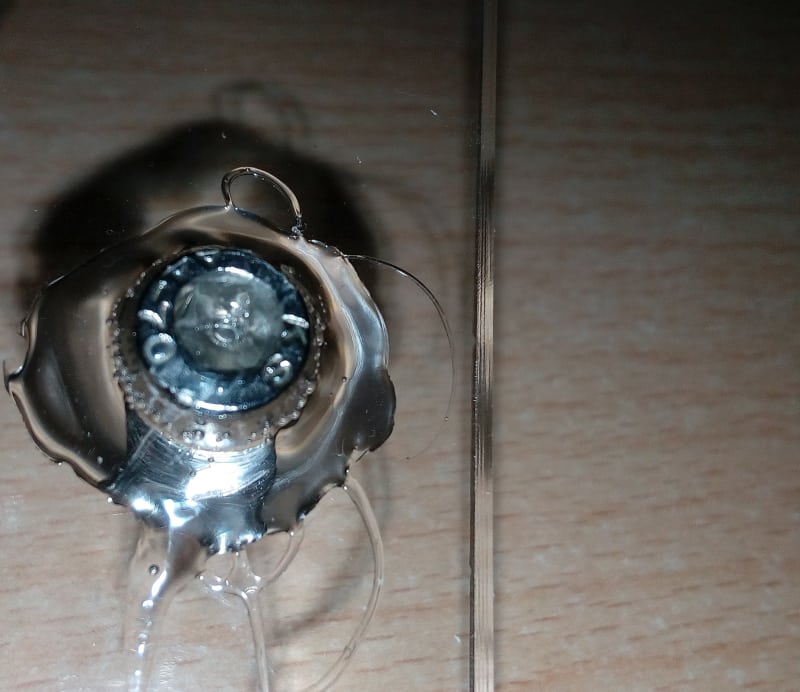
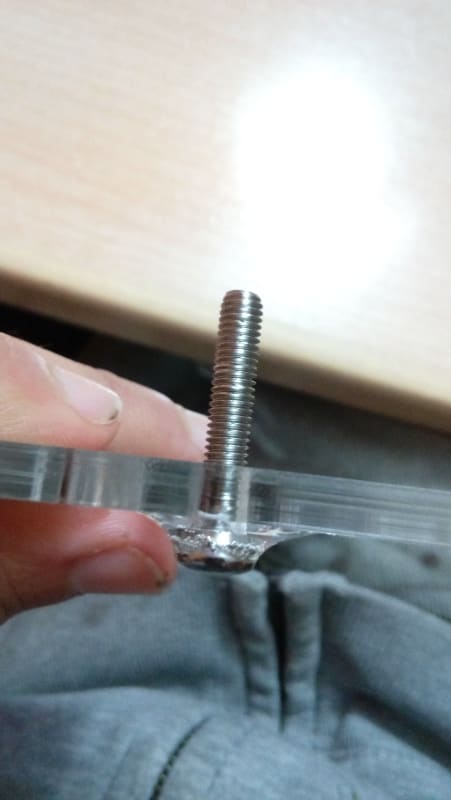
Thank you!!!!!!!!!!!!!!!!!!!