So I am designing some steel structure where exists a bolted joint
The "cylinder" (total 11 tons), is joint by 20 bolts (M22 10.9 grade bolts) to the "frame" or beams (S275 steel, HE 180M profiles).
The FEM simulation is predicting high Von Mises stress in the joints holes and the bolts themselfs
I have used two softwares: Catia v5 using virtual bolts and Simscale using actual 3D bolts (bonded contact)
Catia: (virtual bond)
Simscale (bolt in CAD). Here, max VM is 1880 MPa!
However, I made some calculations following Eurocode 3, and the results are it is safe even using only 2 bolts:
I calculate the "Ed" values like this: I am assuming only using 2 bolts (conservative side)
So then each bolt is suffering some tension force Ft and Shear force Fv. Easy to get
Then, I follow the technical code:
Rd values (resistance) are higher than the actual Ed values. Just "Combination" is >1, but it´s pretty close, and you have to consider my structure has 20 bolts, no 2
Do you have any thoughts why is the FEM predicting so high stress in the area?
Thank you,
regards
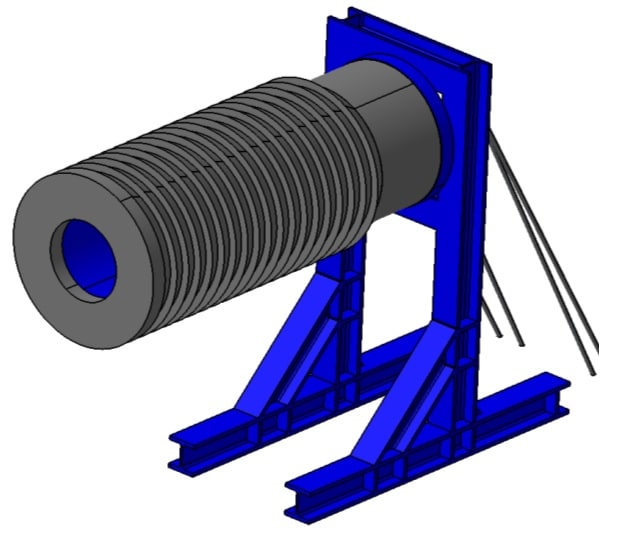
The "cylinder" (total 11 tons), is joint by 20 bolts (M22 10.9 grade bolts) to the "frame" or beams (S275 steel, HE 180M profiles).
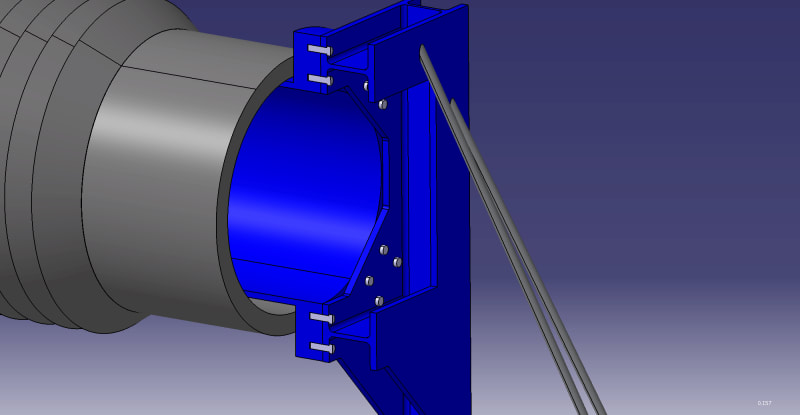
The FEM simulation is predicting high Von Mises stress in the joints holes and the bolts themselfs
I have used two softwares: Catia v5 using virtual bolts and Simscale using actual 3D bolts (bonded contact)
Catia: (virtual bond)
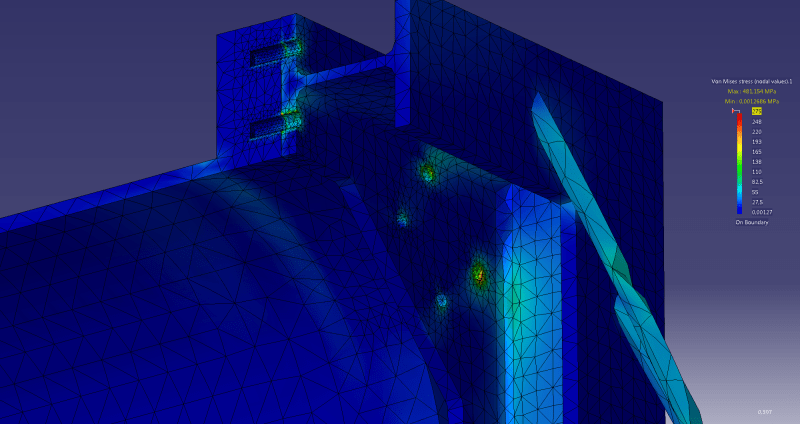
Simscale (bolt in CAD). Here, max VM is 1880 MPa!
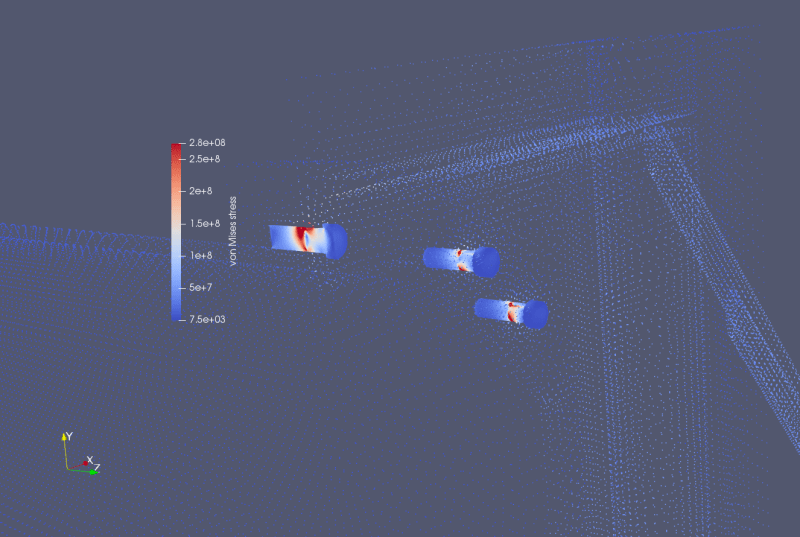
However, I made some calculations following Eurocode 3, and the results are it is safe even using only 2 bolts:
I calculate the "Ed" values like this: I am assuming only using 2 bolts (conservative side)
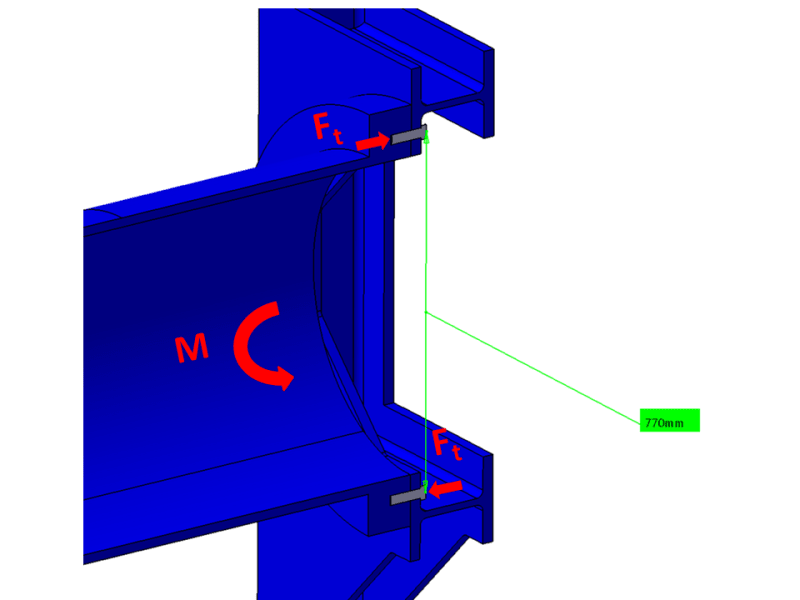
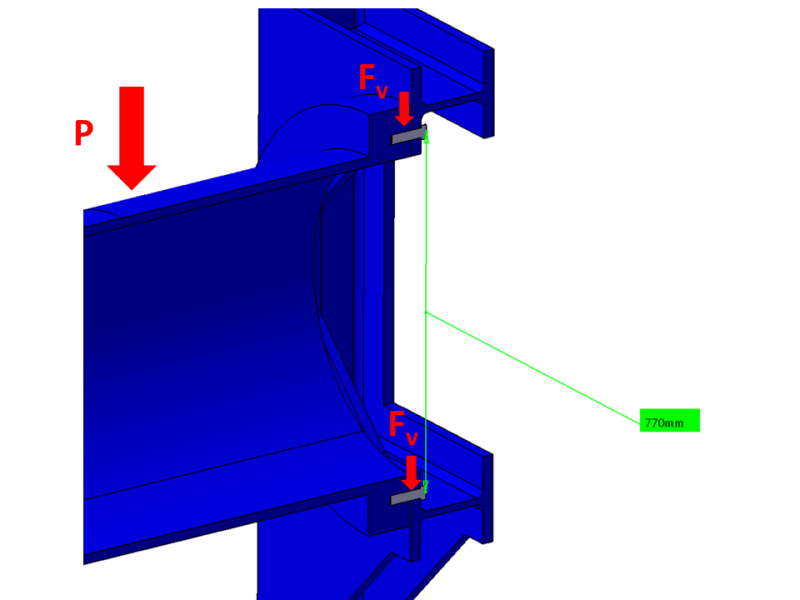
So then each bolt is suffering some tension force Ft and Shear force Fv. Easy to get
Then, I follow the technical code:

Rd values (resistance) are higher than the actual Ed values. Just "Combination" is >1, but it´s pretty close, and you have to consider my structure has 20 bolts, no 2
Do you have any thoughts why is the FEM predicting so high stress in the area?
Thank you,
regards