MFJewell
Mechanical
- Mar 2, 2017
- 366
I am looking at adding a work platform for some control valves at one of our facilities. After several iterations, I am going with a hanging platform that is supported by existing structural steel roof beams. This appears to be the best solution based on congestion in the area. That said, I am undecided on welding the vertical supports or using a bolted connection to attach the vertical supports to the W12/W16. The vertical supports are W6 beams that I plan to attach to the bottom flange of the existing beams. Most of the reference material I have covers beam to beam connections using the web and then beam to column connections using the flanges. Anyone have any insight or advice for this particular application.
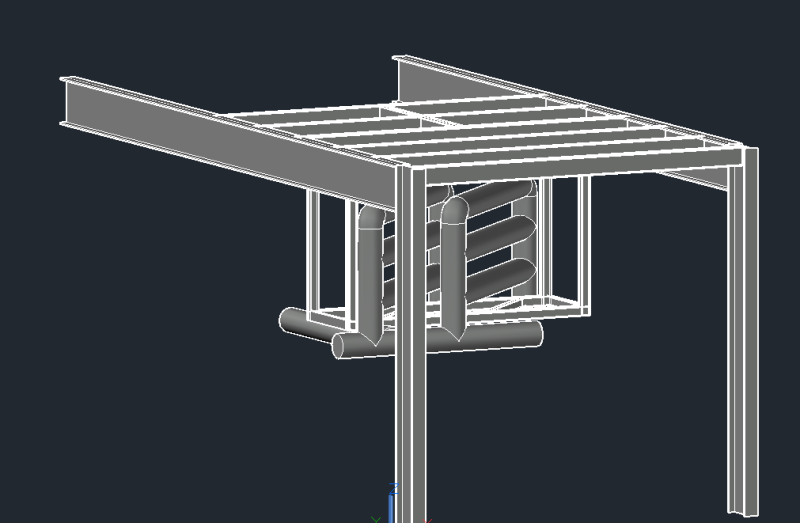
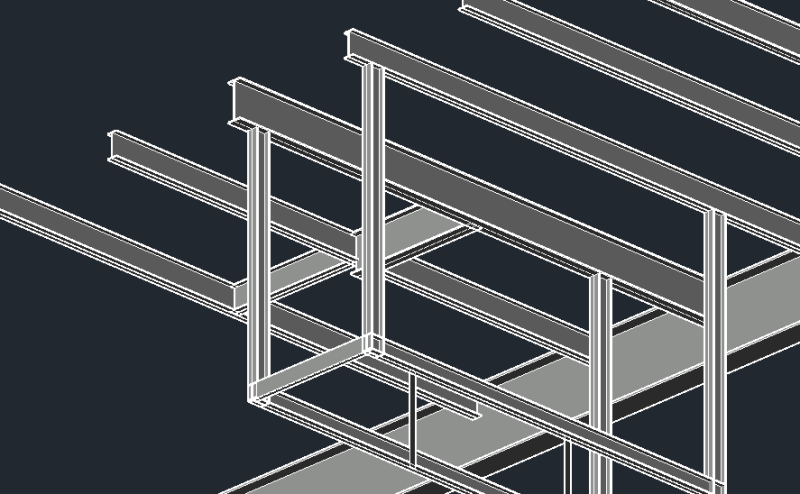
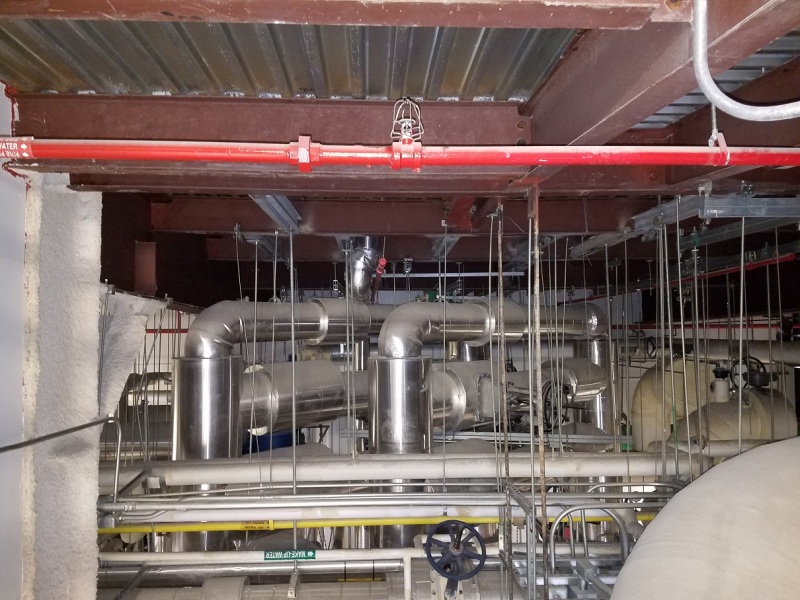