DesignDad
Mechanical
- Apr 26, 2017
- 11
Hello all,
First time post, long time reader.
I am designing IP65 Electrical Enclosure with 80w internal Heat load. It is small and dont have a lot of room for vents, the only IP65 vents I see are made for large off the shelf enclosures.
I have 2 questions:
1. What is the external solar load I need to consider?
2. Calculate Internal Air temp with fan, inside of sealed enclosure?
See my Calculation Page as an attached file, it is based on surface area of the enclosure, plus the additional area of the fins that are cut into the side.
See also, the box geometry here,
Current Calc Sheet that I have going
Chart for Solar Heat Gain
Thanks for all of the help!
First time post, long time reader.
I am designing IP65 Electrical Enclosure with 80w internal Heat load. It is small and dont have a lot of room for vents, the only IP65 vents I see are made for large off the shelf enclosures.
I have 2 questions:
1. What is the external solar load I need to consider?
Based on charts below, aluminum enclosure, clear anodized, with 20deg delta T between ambient and internal, should not have a solar heat gain. Correct?
2. Calculate Internal Air temp with fan, inside of sealed enclosure?
What is the best way to calculate cooling effects in a sealed, small enclosure(12in x 8in x 6in )
Most of the cooling effect comes from the temperature differential but I want to quantify the air movement effects and if increasing the fan flow rate would improve cooling 20-30%
See my Calculation Page as an attached file, it is based on surface area of the enclosure, plus the additional area of the fins that are cut into the side.
See also, the box geometry here,
Current Calc Sheet that I have going
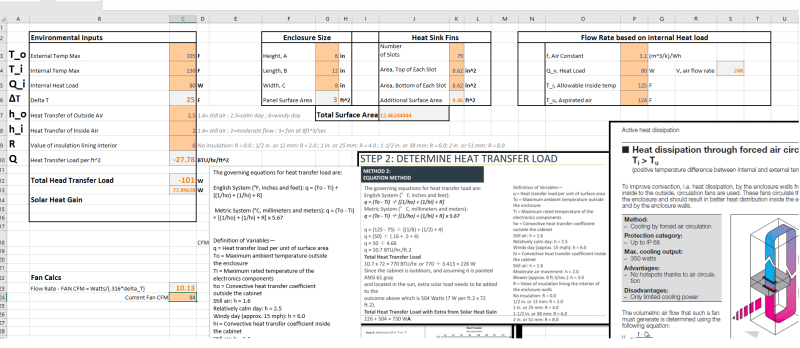
Chart for Solar Heat Gain
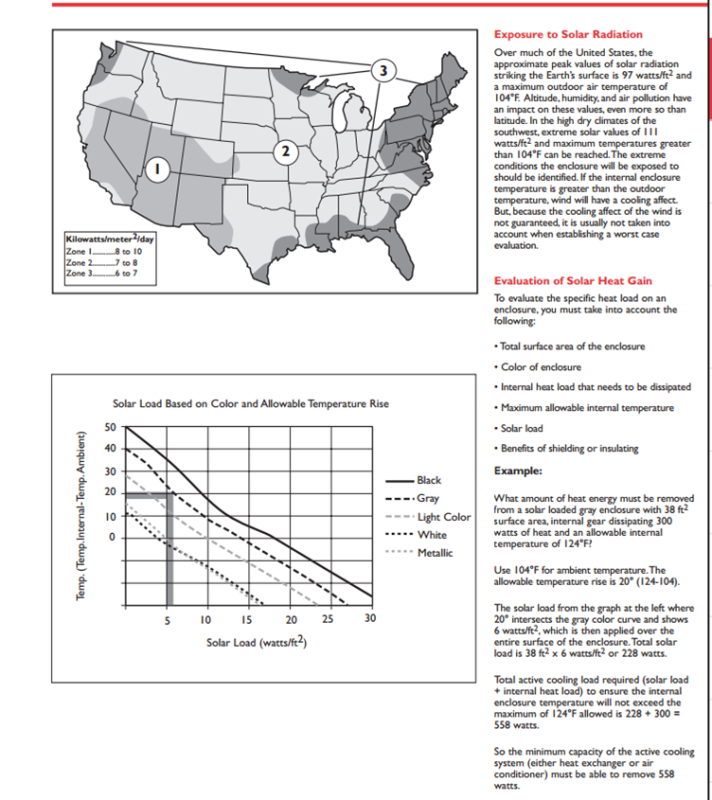
Thanks for all of the help!