kenshin305
Industrial
Hello, I’m an industrial engineering undergrad who is making my own stainless 440C hole saws from 1 inch OD round bar. Using a lathe, I drilled, reamed, and finally used a boring bar to get the wall thickness to 0.021” (I know, it’s very thin). I then used a mill and a v-cutter to machine the teeth. Next, I heat treatment the hole saw to get a martensitic structure. I heat treated at 1038 degrees Celsius for 30 minutes, removed and air quenched, and finally temper for 1 hour at 230 degrees Celsius.
This hole saw was designed to be attached to a T-handle, to manually cut hardwood up to a ¼ inch thick. It cannot rust, and must have high hardness and toughness, which is why I chose 440C. This hole saw worked well for a year. I recently let a friend try it and it broke (see attached pictures). My friend used way more downward force than me when it broke. I feel that my hole saw has way too much hardness (no wear on teeth) but not enough toughness, almost like glass.
Can someone please advise on how to preventing my hole saws from shattering? Many of my engineering professors are baffled.
This hole saw was designed to be attached to a T-handle, to manually cut hardwood up to a ¼ inch thick. It cannot rust, and must have high hardness and toughness, which is why I chose 440C. This hole saw worked well for a year. I recently let a friend try it and it broke (see attached pictures). My friend used way more downward force than me when it broke. I feel that my hole saw has way too much hardness (no wear on teeth) but not enough toughness, almost like glass.
Can someone please advise on how to preventing my hole saws from shattering? Many of my engineering professors are baffled.
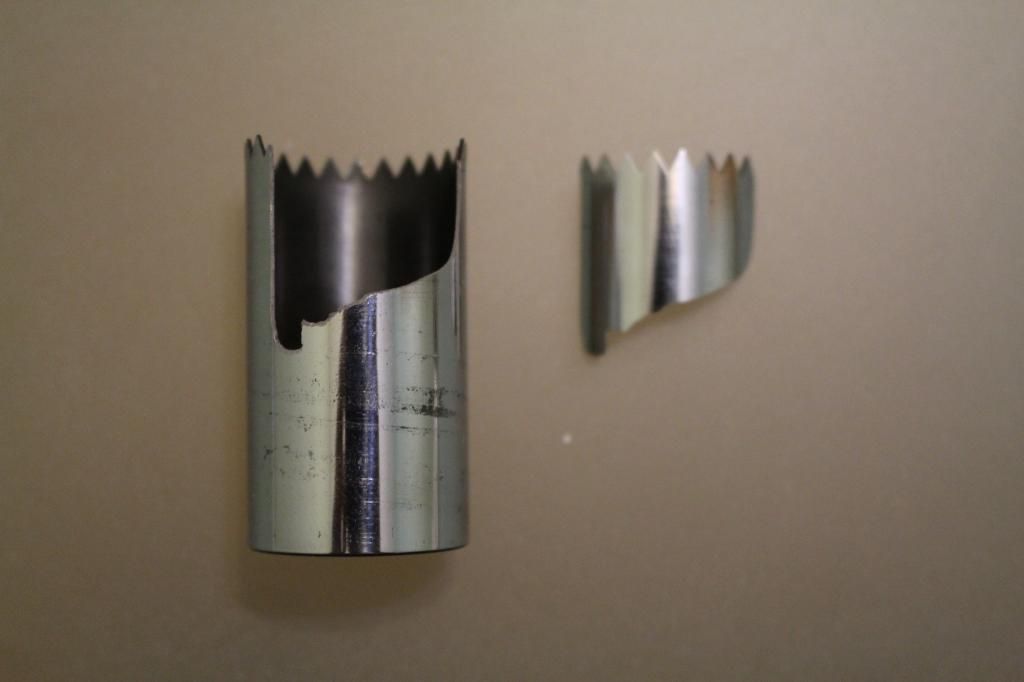
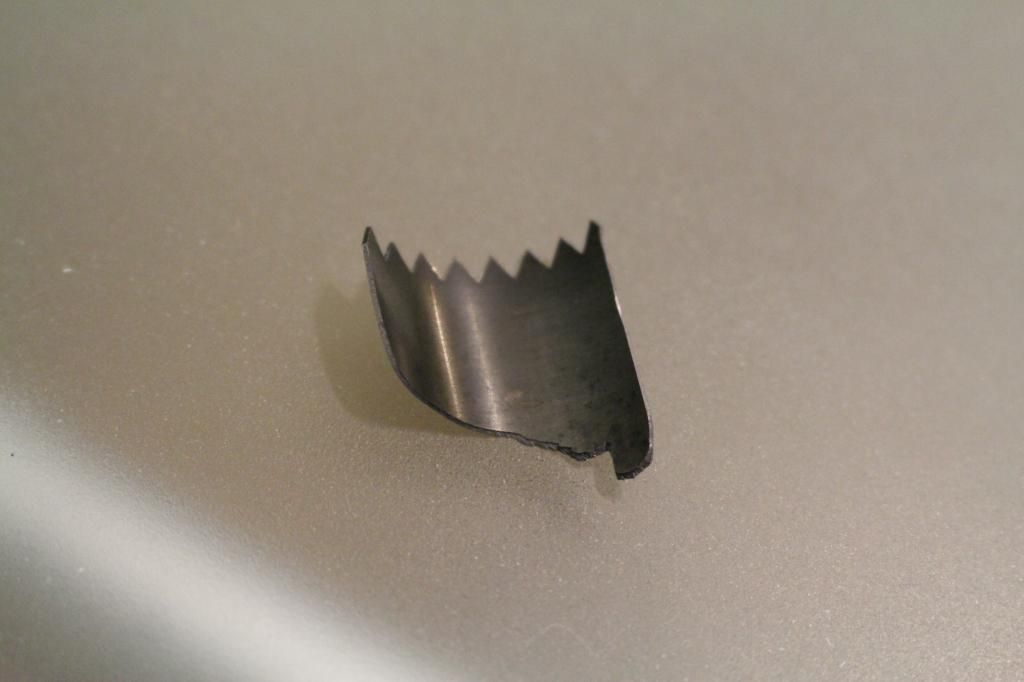

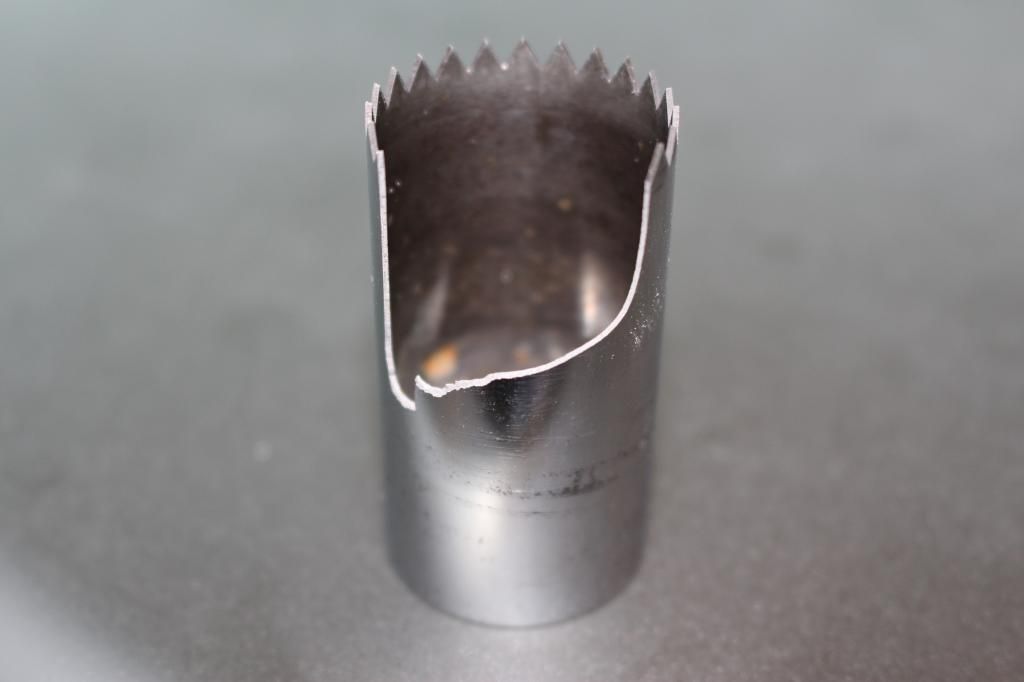
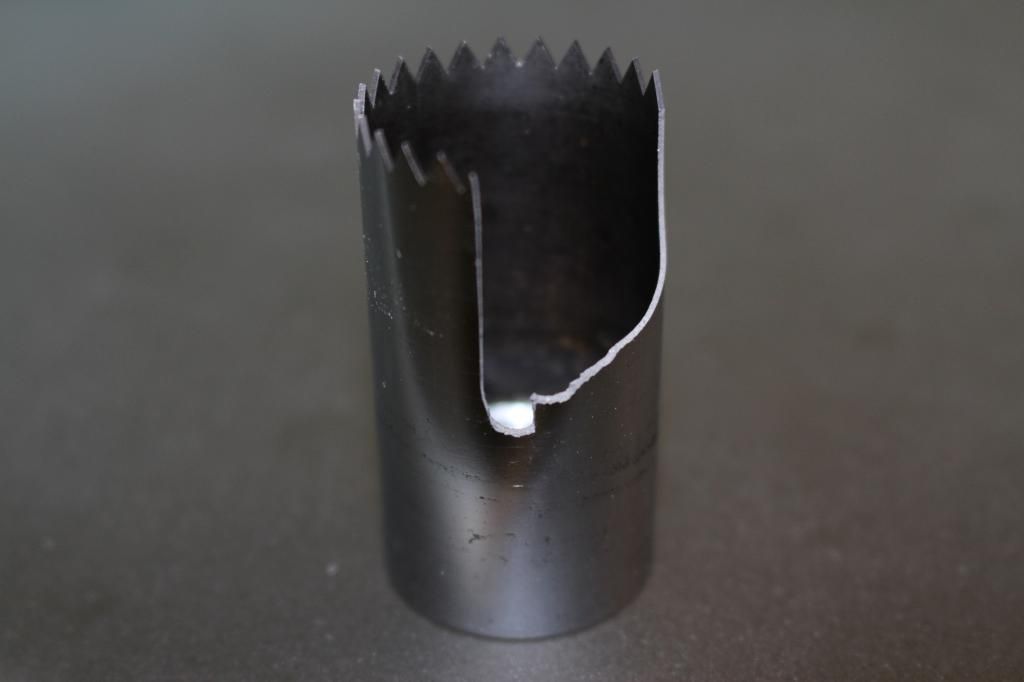