J_04051988
Petroleum
The problem is that I have low allowable values for this pump. The ideal would be to put a fixed point where I indicate so that it absorbs the force of the water hammer, but it created very high stresses in the pump connection.
It would be correct to use an expansion joint with a double nut like the one attached in the image. On the one hand it would have the tie rods to absorb the equivalent pressure and on the other hand the inner nut to absorb the water hammer.
If I use an axial joint without tie rods I have equivalent pressure in the connection.
What could be another solution?
thank you anyway
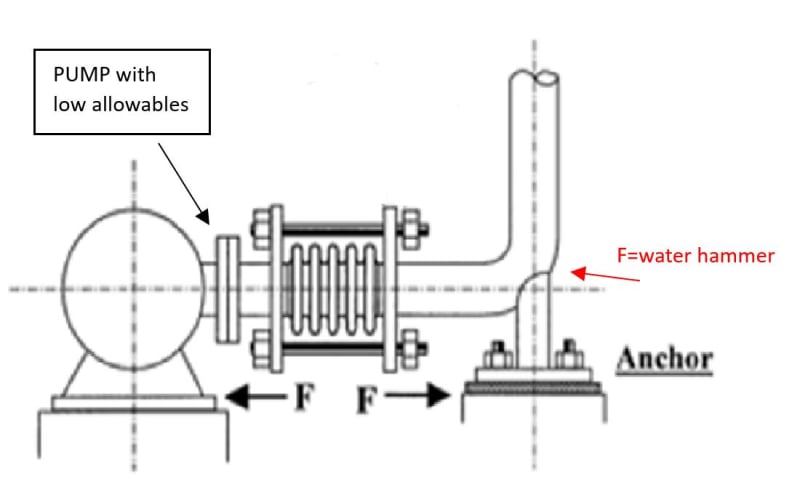
It would be correct to use an expansion joint with a double nut like the one attached in the image. On the one hand it would have the tie rods to absorb the equivalent pressure and on the other hand the inner nut to absorb the water hammer.
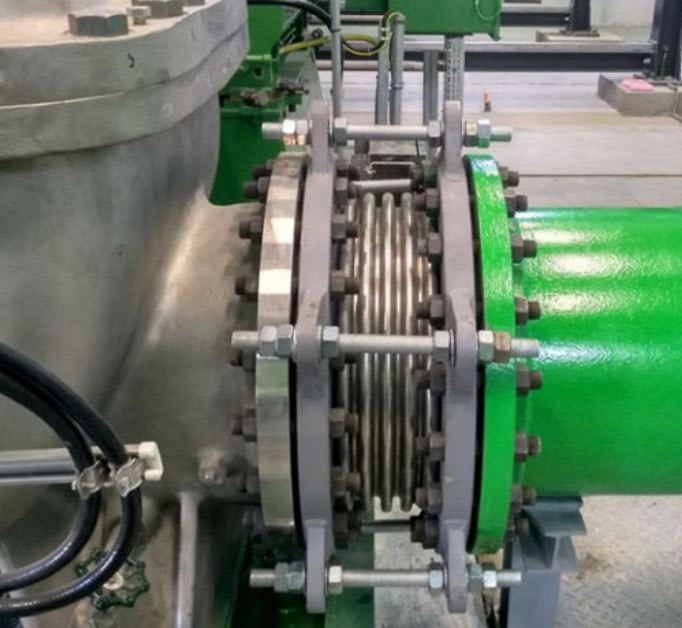
If I use an axial joint without tie rods I have equivalent pressure in the connection.
What could be another solution?
thank you anyway