ehbadger
Chemical
- Oct 7, 2015
- 119
I have some reactors in a corrosive service. Heads are 30" 300# flanges. They were installed with studs. See attached photos
The corrosion between the stud shaft and flange itself locks it up tighter than whatever you can think of that is really damn tight. We can get both nuts to break free but that is actually not helpful as the stud is still "frozen" in place. Also note, the only way to get the stud out is to remove the bottom nut and pull the stud out from the top. We cannot go down because there is no clearance between the flange and vessel itself. Cutting isn't very useful either.
We tried to weld the top nuts to the studs to create what is effectively a bolt. Tack welds at first (didn't work) so we went back around and did the whole circumference. However we are actually shearing the welds with the big torque gun and still not breaking the stud loose. We've tried a ~3/8" interference pin in a hole drilled half and half into stud and nut, which worked for a few, but that is rolling over and not working in most. We tried a hole and pin though the side of the nut into the shaft (shear pin style) but that is shearing as well.
We've got 32 bolts per flange, 3 on each vessel. Drilling 3/8"+ holes for pins/keys is very time consuming and kills a serious amount of drill bits.
Next plan of attack is some hot welding and trying to burn down between nuts and stud and get more area fused. This is also pretty undesireable (but not impossible) due to it being some serious hot work in the middle of a turnaround.
Any creative ideas out there?
Note: For reassembly I am using PTFE coated BOLTS. (not the crappy ptfe coated ones either)
The corrosion between the stud shaft and flange itself locks it up tighter than whatever you can think of that is really damn tight. We can get both nuts to break free but that is actually not helpful as the stud is still "frozen" in place. Also note, the only way to get the stud out is to remove the bottom nut and pull the stud out from the top. We cannot go down because there is no clearance between the flange and vessel itself. Cutting isn't very useful either.
We tried to weld the top nuts to the studs to create what is effectively a bolt. Tack welds at first (didn't work) so we went back around and did the whole circumference. However we are actually shearing the welds with the big torque gun and still not breaking the stud loose. We've tried a ~3/8" interference pin in a hole drilled half and half into stud and nut, which worked for a few, but that is rolling over and not working in most. We tried a hole and pin though the side of the nut into the shaft (shear pin style) but that is shearing as well.
We've got 32 bolts per flange, 3 on each vessel. Drilling 3/8"+ holes for pins/keys is very time consuming and kills a serious amount of drill bits.
Next plan of attack is some hot welding and trying to burn down between nuts and stud and get more area fused. This is also pretty undesireable (but not impossible) due to it being some serious hot work in the middle of a turnaround.
Any creative ideas out there?
Note: For reassembly I am using PTFE coated BOLTS. (not the crappy ptfe coated ones either)
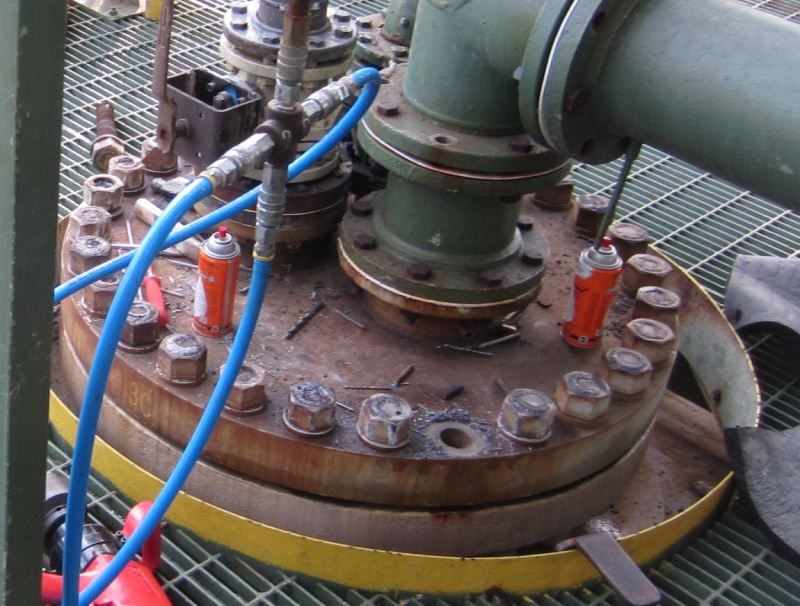
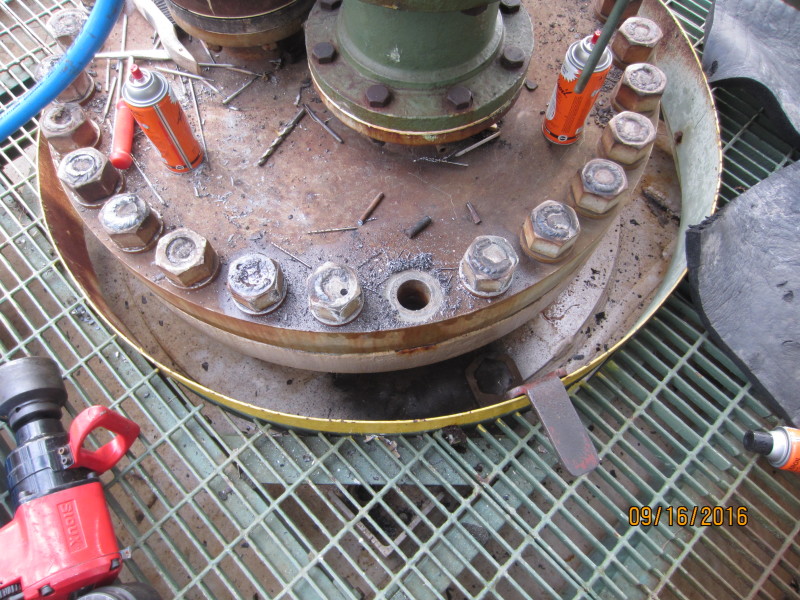