Burner2k
Aerospace
- Jun 13, 2015
- 193
Here is the setup of my problem. I have a projectile which is being launched from a tube. I need to do a static analysis on the projectile. Objective is to ascertain integrity of the structure during launch. I have quasi-static loads (in terms of Gs) which the projectile will experience at the time of the launch.
I have modeled the structure will shell elements and have created a node at the CG. A RBE3 connects from the CG node (dependent) to the shell elements (independent). I am the acceleration as a force (mass x g) on the CG.
Trying to do a linear Static Solution (101) using Auto Inertia Relief. The issue is that NASTRAN wants to apply balancing accelerations on the CG itself and since NASTRAN does not allow RBE3 dependent nodes to have any SPCs, I am getting Fatal Error messages.
Since Inertia Relief does not support Grav cards (actually it doesn't give any errors but only zero deflections), that option is also ruled out.
I guess for now, I'll create another node near CG & make that node the dependent of RBE3 & apply my force on that node.
But I would like to hear on alternate approach to accomplish the above analysis.
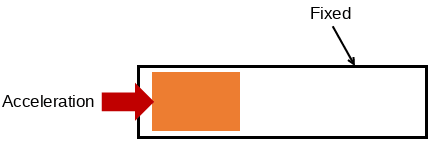
I have modeled the structure will shell elements and have created a node at the CG. A RBE3 connects from the CG node (dependent) to the shell elements (independent). I am the acceleration as a force (mass x g) on the CG.
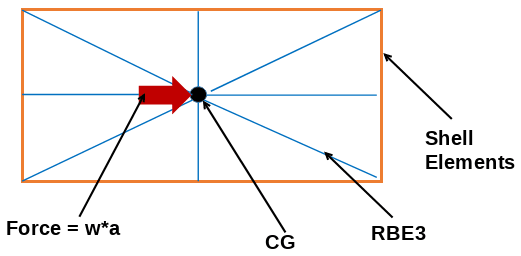
Trying to do a linear Static Solution (101) using Auto Inertia Relief. The issue is that NASTRAN wants to apply balancing accelerations on the CG itself and since NASTRAN does not allow RBE3 dependent nodes to have any SPCs, I am getting Fatal Error messages.
Since Inertia Relief does not support Grav cards (actually it doesn't give any errors but only zero deflections), that option is also ruled out.
I guess for now, I'll create another node near CG & make that node the dependent of RBE3 & apply my force on that node.
But I would like to hear on alternate approach to accomplish the above analysis.