Hey All,
I have a formed sheet metal part similar to that shown. Dataum A is the flat back surface, Datum B is defined by a hole perpendicular to A. Datum C is defined as the center plane of a slot. I want the ears of the sheet metal part to by symmetric to a center plane running through the center or the part. I know that you don't use Symmetry, so I want to call it out with Position tolerance. What are you thoughts of creating a Datum D which is the center plane bewteen the hole and the slot? This is off of a basic dimension which is kinda weird to me. Or, any other way to set this up so that the ears are located by a Position tolerance relative to a center plane?
Thanks for any help!
I have a formed sheet metal part similar to that shown. Dataum A is the flat back surface, Datum B is defined by a hole perpendicular to A. Datum C is defined as the center plane of a slot. I want the ears of the sheet metal part to by symmetric to a center plane running through the center or the part. I know that you don't use Symmetry, so I want to call it out with Position tolerance. What are you thoughts of creating a Datum D which is the center plane bewteen the hole and the slot? This is off of a basic dimension which is kinda weird to me. Or, any other way to set this up so that the ears are located by a Position tolerance relative to a center plane?
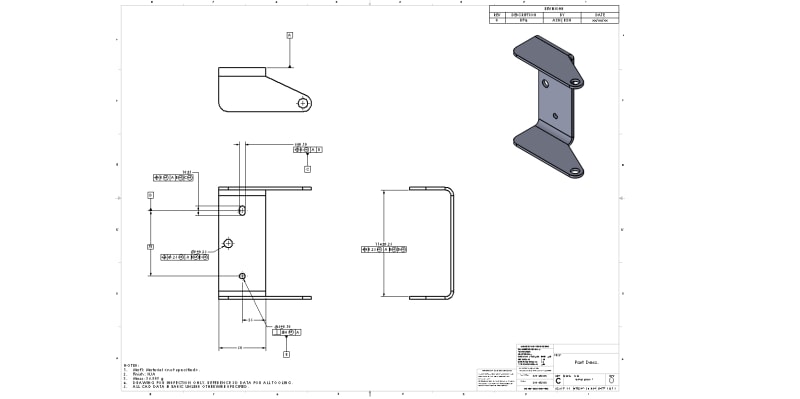
Thanks for any help!