-
1
- #1
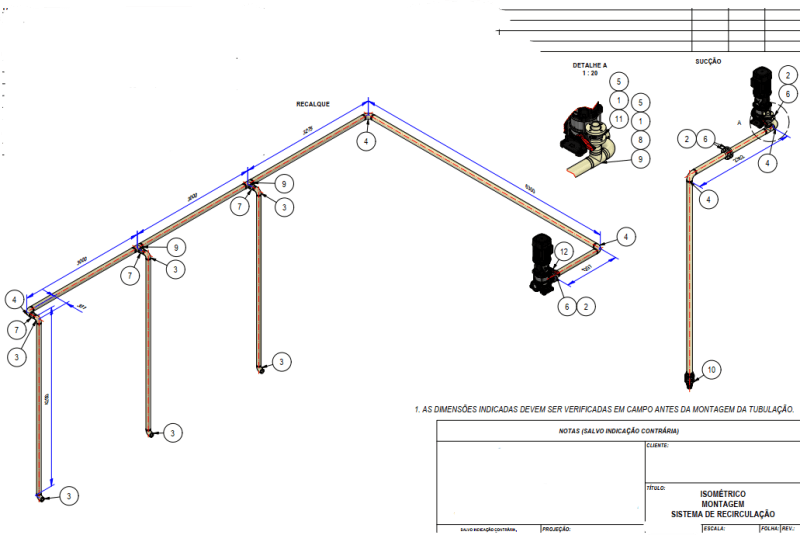
Hi all!
I need help with commissioning this pump. The design engineer is not around anymore and now I'm responsible.
The idea is to use the centrifugal pump to recirculate and agitate the liquid in the tank.
The piping has an internal diameter of 90 mm. I've already made some calculations for the headloss and maximum suction lift accordint to manufacturer's operating manual and concluded that I had to reduce the pump speed, because the headloss was too high. Even with 1750 rpm the pump can't lift the liquid and recirculate.
I'm considering to increase the pipe's ID to 130 mm so maybe I can operate the pump at full speed.
Any thoughts or ideas that I should try before replacing the piping?