Ninjako44
Structural
- Apr 2, 2016
- 2
Dear all,
For the attached long. frame , I took Temperature effect by taking max temp.=+35 and min. temp.=-35, it applied large values of axial load on the struts and the brace which made the model not safe ,consequently i changed the profiles to larger , the axial force increased and so on, reducing the profiles is not good for slenderness. I don't want to depend on the bolt hole tolerances , any suggestions ?
For the attached long. frame , I took Temperature effect by taking max temp.=+35 and min. temp.=-35, it applied large values of axial load on the struts and the brace which made the model not safe ,consequently i changed the profiles to larger , the axial force increased and so on, reducing the profiles is not good for slenderness. I don't want to depend on the bolt hole tolerances , any suggestions ?
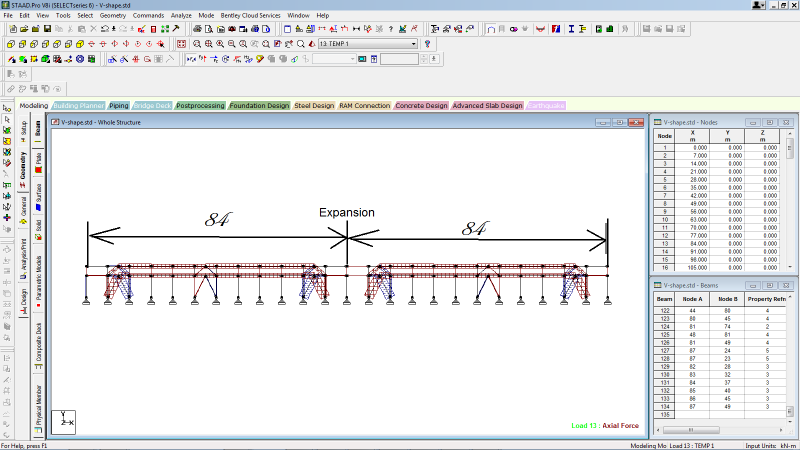