KootK
Structural
- Oct 16, 2001
- 18,563
This thread introduction may well be too long for busy folks to read. If so, you can probably get a pretty good jist of it just by scrolling through the graphics. I won't be lambasting anybody because they bring up something that I have already mentioned in the text.
I've presented some possible solutions below that I would like to have vetted by the gang. Naturally, I would also be utterly thrilled to entertain alternate, better solutions. In my heart of hearts, I'd like to rip out the walls and replace them with the 6" studs that should have been there to begin with. That would not be good client care in this instance however.
THE SITUATION
1) existing 3-5/8" jamb stud for a rather large wall opening in a highrise condo.
2) jamb stud will deliver about 1500 lbs ULS wind shear to its slab connection.
3) jamb stud is already being reinforced with a nested, 3" steel channel.
4) original connection design was some aggressively designed clips and concrete screws.
5) site work has revealed that, in some locations, the slab edge was originally saw cut as shown in the the photo below. Some kind of field error presumably.
6) my hardworking jamb stud connection now has a stud cantilever of up to 2".
7) expensive folks are standing around on site seeking direction.
THE CONSTRAINTS (AT LEAST FOR NOW)
8) Existing wall system is to remain in place during repair. Exterior sheathing will come off.
9) Need a solution that works for stud cantilevers ranging from 1/2" min to 2" max.
10) No field welding.
11) Need to be a little sensitive to building envelope concerns. I can, locally, have a bit of steel that would project into the exterior sheathing/insulation space.
THE OPTIONS CURRENTLY TABLED
OPTION 1. For a short length of slab, feather out the slab edge with repair concrete somehow. This would, ostensibly, be pretty great. Can that be done in such a way that we'd trust that repair concrete to be able to handle the fastener shear loads coming in from the jamb studs though? It gives me the heebee jeebess. I also worry that it's hard to do without removing the existing stud work. I would be interested to hear if this solution is viable and, if it is, recommendations for appropriate materials and procedures.
OPTION 2. This is a clever solution suggested by the client. My main concern with this is the viability of the grouting which would need to work at thicknesses ranging from 1/2" to 2". If the grout is installed before the bolt, will it just fall off during drill & epoxy'ing of the bolt? Would it be feasible to install the bolt first, grout around it, and then attach the angle? Could the bolt and angle be installed first, with the angle kept still somehow, and then grout be stuffed in behind the angle as a final operation?
OPTION 3. Similar to option two but no longer reliant on grouting feasibility. It's just... kinda silly looking. I would like to do something similar with a single back side nut, much like traffic sign structure bases are handled sometimes. Given the access situation, however, is there any way that I could use a single, backside not and be confident that it would be locked in place for the long haul? This would be easier at the 2" dimension and harder at the 1/2" dimension I reckon.
I've presented some possible solutions below that I would like to have vetted by the gang. Naturally, I would also be utterly thrilled to entertain alternate, better solutions. In my heart of hearts, I'd like to rip out the walls and replace them with the 6" studs that should have been there to begin with. That would not be good client care in this instance however.
THE SITUATION
1) existing 3-5/8" jamb stud for a rather large wall opening in a highrise condo.
2) jamb stud will deliver about 1500 lbs ULS wind shear to its slab connection.
3) jamb stud is already being reinforced with a nested, 3" steel channel.
4) original connection design was some aggressively designed clips and concrete screws.
5) site work has revealed that, in some locations, the slab edge was originally saw cut as shown in the the photo below. Some kind of field error presumably.
6) my hardworking jamb stud connection now has a stud cantilever of up to 2".
7) expensive folks are standing around on site seeking direction.
THE CONSTRAINTS (AT LEAST FOR NOW)
8) Existing wall system is to remain in place during repair. Exterior sheathing will come off.
9) Need a solution that works for stud cantilevers ranging from 1/2" min to 2" max.
10) No field welding.
11) Need to be a little sensitive to building envelope concerns. I can, locally, have a bit of steel that would project into the exterior sheathing/insulation space.
THE OPTIONS CURRENTLY TABLED
OPTION 1. For a short length of slab, feather out the slab edge with repair concrete somehow. This would, ostensibly, be pretty great. Can that be done in such a way that we'd trust that repair concrete to be able to handle the fastener shear loads coming in from the jamb studs though? It gives me the heebee jeebess. I also worry that it's hard to do without removing the existing stud work. I would be interested to hear if this solution is viable and, if it is, recommendations for appropriate materials and procedures.
OPTION 2. This is a clever solution suggested by the client. My main concern with this is the viability of the grouting which would need to work at thicknesses ranging from 1/2" to 2". If the grout is installed before the bolt, will it just fall off during drill & epoxy'ing of the bolt? Would it be feasible to install the bolt first, grout around it, and then attach the angle? Could the bolt and angle be installed first, with the angle kept still somehow, and then grout be stuffed in behind the angle as a final operation?
OPTION 3. Similar to option two but no longer reliant on grouting feasibility. It's just... kinda silly looking. I would like to do something similar with a single back side nut, much like traffic sign structure bases are handled sometimes. Given the access situation, however, is there any way that I could use a single, backside not and be confident that it would be locked in place for the long haul? This would be easier at the 2" dimension and harder at the 1/2" dimension I reckon.

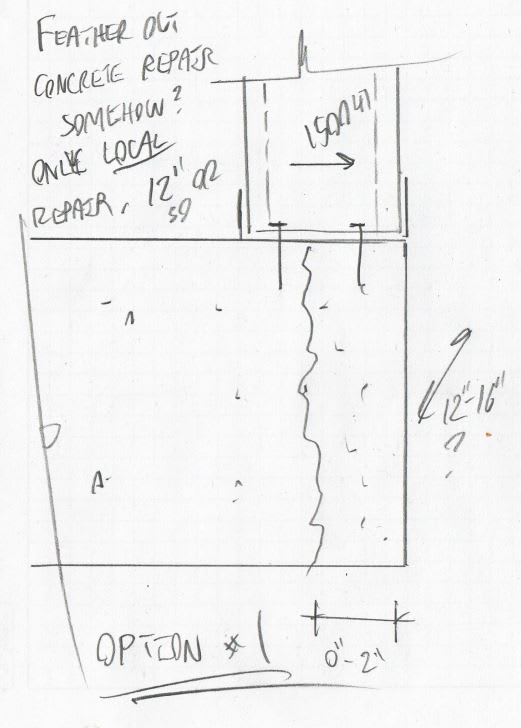
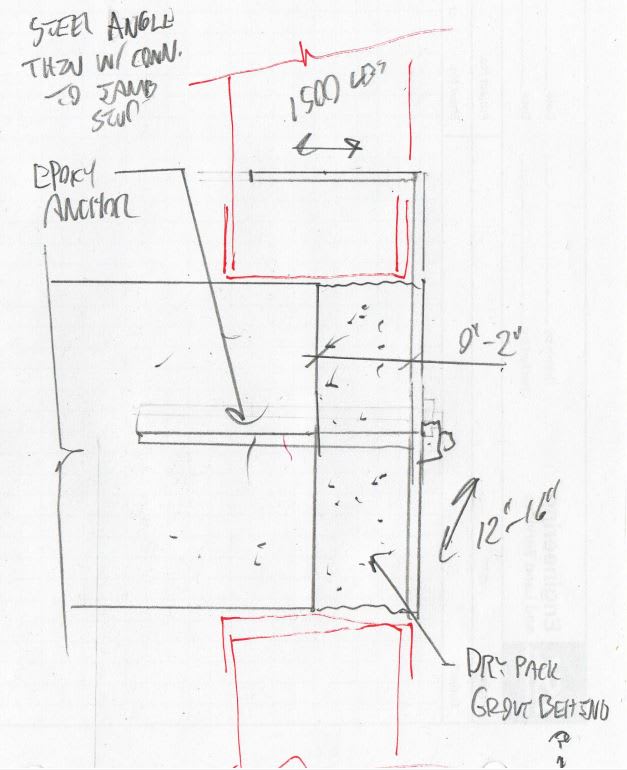
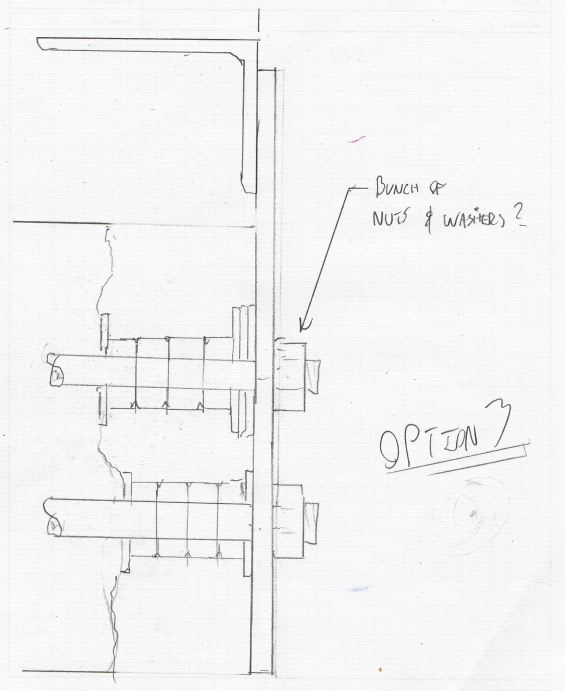
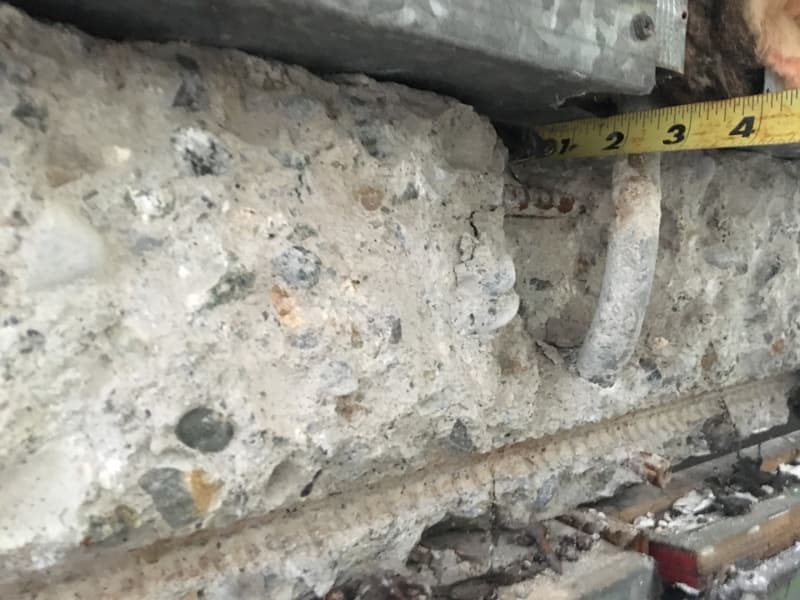