A8yssUK
Industrial
- Apr 7, 2014
- 56
Hi all I am looking at building a testing device. See simple image.
To measure leakage of helium from a test device with internal volume (V1) upto 200 bar with helium. (no explodey gases)
I want to use use our Helium Mass Spectrometer (HeMS) in full vacuum mode so I'd like a vacuum chamber around the test volume (V2).
Now V1 is a test device which may fail and blow out into V2. So I will have a blowout valve (Bout) on V2 to prevent it pressuring above 0.2 bar and a control on the pressure in (Pin).
The HeMS also has over-pressure protection and the blow out will be directed into a well ventilated lab or directly outside.
So does V2 only need to be rated for just vacuum to 0.2 bar or does it need to be rated higher to contain all of the V1 pressure if for some reason Bout fails ?
V1 will be around 30-40L. I am in Europe so it should be PED certified.
I have a similar setup already... but using much lower volumes (V1 < 1L) so not much risk of blowing anything up...
Thanks for any thoughts!
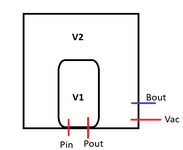
To measure leakage of helium from a test device with internal volume (V1) upto 200 bar with helium. (no explodey gases)
I want to use use our Helium Mass Spectrometer (HeMS) in full vacuum mode so I'd like a vacuum chamber around the test volume (V2).
Now V1 is a test device which may fail and blow out into V2. So I will have a blowout valve (Bout) on V2 to prevent it pressuring above 0.2 bar and a control on the pressure in (Pin).
The HeMS also has over-pressure protection and the blow out will be directed into a well ventilated lab or directly outside.
So does V2 only need to be rated for just vacuum to 0.2 bar or does it need to be rated higher to contain all of the V1 pressure if for some reason Bout fails ?
V1 will be around 30-40L. I am in Europe so it should be PED certified.
I have a similar setup already... but using much lower volumes (V1 < 1L) so not much risk of blowing anything up...
Thanks for any thoughts!
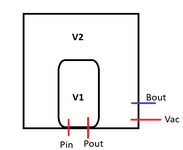