Hi everyone,
Most guidelines I read mention it's possible to model aluminum honeycombs as 2D Orthotropic. Taking a look at manufacturers datasheets, I feel the properties force us to use 3D Orthotropic. But I'm not sure and I'd like your opinion. For example, the properties below are from Hexcel HexWeb. Look how I put those properties in the Femap 3D Orthotropic Material card. Is it correct? Is it a problem to have E1 = E2 = G12 = v23 = v13 = 0?
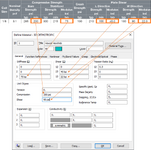
And also, if I were to model this honeycomb as a 2D Orthotropic material, would it be ok to use the properties like below? Notice I use E1 = E2 = very low value, because the in-plane stiffness of sandwich comes from the facesheets. Doesn't it result in wrong values not having the compressive modulus value of 75 ksi in the material card properties? Also, is it ok to leave G12 = 0?
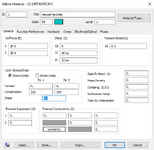
Most guidelines I read mention it's possible to model aluminum honeycombs as 2D Orthotropic. Taking a look at manufacturers datasheets, I feel the properties force us to use 3D Orthotropic. But I'm not sure and I'd like your opinion. For example, the properties below are from Hexcel HexWeb. Look how I put those properties in the Femap 3D Orthotropic Material card. Is it correct? Is it a problem to have E1 = E2 = G12 = v23 = v13 = 0?
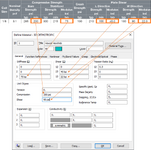
And also, if I were to model this honeycomb as a 2D Orthotropic material, would it be ok to use the properties like below? Notice I use E1 = E2 = very low value, because the in-plane stiffness of sandwich comes from the facesheets. Doesn't it result in wrong values not having the compressive modulus value of 75 ksi in the material card properties? Also, is it ok to leave G12 = 0?
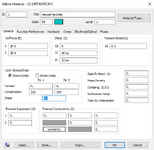
Last edited: