Doodler3D
Mechanical
- Jan 20, 2020
- 188
Hi,
Would it be appropriate to use the Janssen or Jenike equations to calculate the vertical and wall pressure at the base below the extrusion screw? I'm assuming the presence of the screw blades would increase surface area and significantly decrease the vertical pressure on the base. A hydrostatic assumption leads to design failure and additional reinforcement.
Thank you
Would it be appropriate to use the Janssen or Jenike equations to calculate the vertical and wall pressure at the base below the extrusion screw? I'm assuming the presence of the screw blades would increase surface area and significantly decrease the vertical pressure on the base. A hydrostatic assumption leads to design failure and additional reinforcement.
Thank you
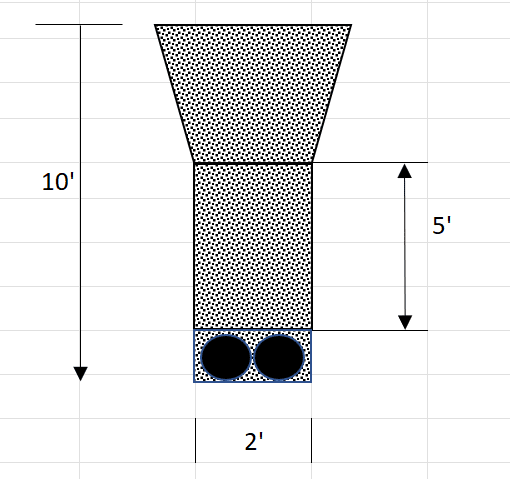