Hello,
I was tasked to design a standardized guided banded pipe saddle. Our worst case simulation models from AutoPIPE are coming up with large ratios of horizontal to vertical loads, so we are investigating overturning as an issue. With the numbers we came up with, it seems to prevent the worst case overturning from all realistic client pipe classes/situations, we would have to use very wide base plates which are unrealistic for pipe spacing requirements. Now we are looking at how the friction of the saddle band against the pipe might help prevent overturning. Assuming the saddle would rotate around the very outer corner of the base plate, my project manager suggested using the equations/method below. I was wondering if this was an oversimplified approach. I realize frictional force is calculated by F=µN, however it is not a single point of contact and I feel there should be some kind of angular component or something involved. It seems from an internet search that the formulas for disk breaks etc. are more somplicated, and while it's a different problem it's still friction on metal stopping the rotation of metal. Am I over complicating this?
Here is a side view so that you can see how the bands attach. Thanks
I was tasked to design a standardized guided banded pipe saddle. Our worst case simulation models from AutoPIPE are coming up with large ratios of horizontal to vertical loads, so we are investigating overturning as an issue. With the numbers we came up with, it seems to prevent the worst case overturning from all realistic client pipe classes/situations, we would have to use very wide base plates which are unrealistic for pipe spacing requirements. Now we are looking at how the friction of the saddle band against the pipe might help prevent overturning. Assuming the saddle would rotate around the very outer corner of the base plate, my project manager suggested using the equations/method below. I was wondering if this was an oversimplified approach. I realize frictional force is calculated by F=µN, however it is not a single point of contact and I feel there should be some kind of angular component or something involved. It seems from an internet search that the formulas for disk breaks etc. are more somplicated, and while it's a different problem it's still friction on metal stopping the rotation of metal. Am I over complicating this?
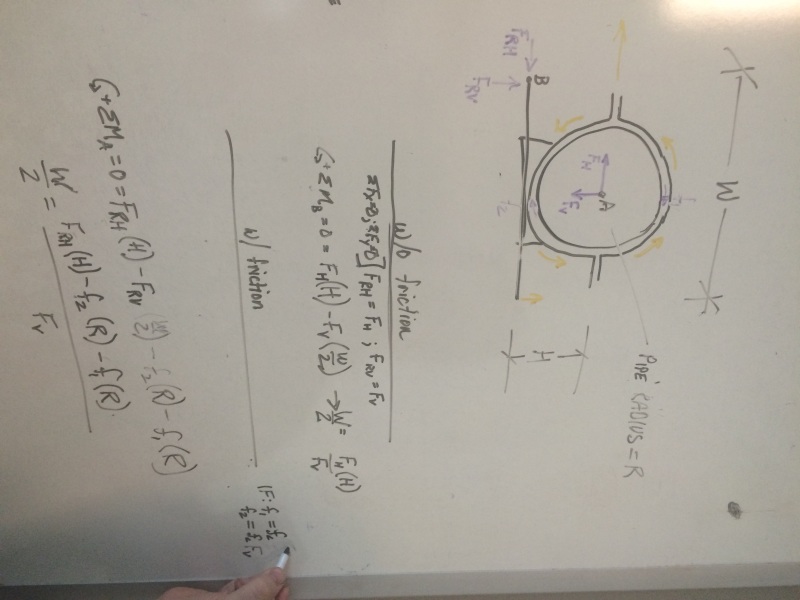
Here is a side view so that you can see how the bands attach. Thanks
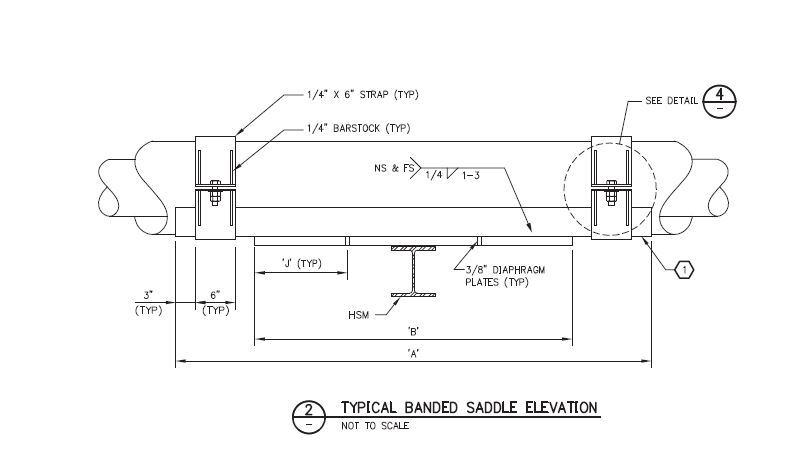