7788_011
Structural
- Feb 7, 2022
- 24
Hello,
Below is the plan view of roof structure for a residential jobs, which is 6m x 9.4m x 4m high.
The yellow lines you are seeing is the c purlins @ 1200 cts while the blue ones are rafters.
Wall bracings are placed under rafters and structs
Now I have an horizontal deflection issue about the red ones which are struts (or wind beams if you call it this way) on the external walls because the external wall thickness is limited to 90mm, which means the width of the strut member is limited to 90mm only.
Below is the plan view of roof structure for a residential jobs, which is 6m x 9.4m x 4m high.
The yellow lines you are seeing is the c purlins @ 1200 cts while the blue ones are rafters.
Wall bracings are placed under rafters and structs
Now I have an horizontal deflection issue about the red ones which are struts (or wind beams if you call it this way) on the external walls because the external wall thickness is limited to 90mm, which means the width of the strut member is limited to 90mm only.
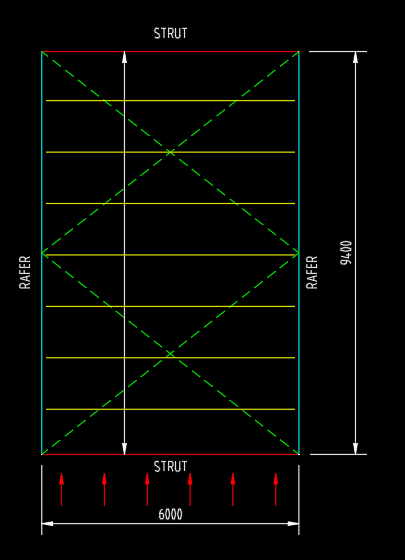