Cpw628
Structural
- Jan 18, 2024
- 10
I am looking at a pipe rack that is going to add a new pipe with ASCE 7-16 loads. There has been discussion in my office about how to apply the non-structural pipe loads to the rack. Because it is ASME piping, the R factor per ASCE 7 Chapter 13 is 12. This compares to the R factor of 1 for the frame per Chapter 15. This means that the Ch 15 loads are over 3 times greater than Ch 13.
The question is, can we use the smaller loads to capture the local stresses on the frame? Below is an image with the new pipe in red and the blue column is the member who's stresses are of concern. With the smaller Ch 13 loads, the blue beam is under a 10% increase in weak axis bending and torsion, but with Ch 15 loads, it increases to about 20%.
The question is, can we use the smaller loads to capture the local stresses on the frame? Below is an image with the new pipe in red and the blue column is the member who's stresses are of concern. With the smaller Ch 13 loads, the blue beam is under a 10% increase in weak axis bending and torsion, but with Ch 15 loads, it increases to about 20%.
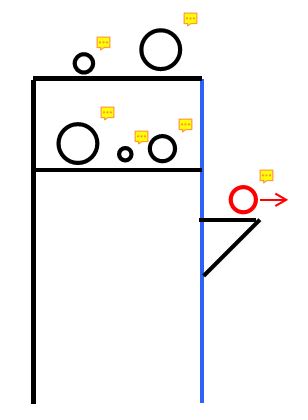