RanjanC
Chemical
- Sep 21, 2015
- 3
We have a scheme where Lean Amine Pump discharges to a high pressure Amine Contactor. There is dual check valve near the amine inlet to column to prevent high pressure gas back flow to amine circuit in case of lean amine pump trip. In the HAZOP analysis, a scenario came where the lean amine stops and check valve leaks to pressurise 150# rating suction of Lean amine pump. It may be noted that lean amine pump has a booster pump with its check valve. What we thought that any small leakage of amine from the Amine column upstream of dual check valve can pressurise the upstream amine section if it is 100% liquid full.
My questions
a) Is liquid pipe in pump discharge always 100% full of liquid?
b) Can any voidage be assumed for liquid fill pipe to accept back pressure of additional amine pushed through the dual check valves by high pressure gas?
Thanks
RC
My questions
a) Is liquid pipe in pump discharge always 100% full of liquid?
b) Can any voidage be assumed for liquid fill pipe to accept back pressure of additional amine pushed through the dual check valves by high pressure gas?
Thanks
RC
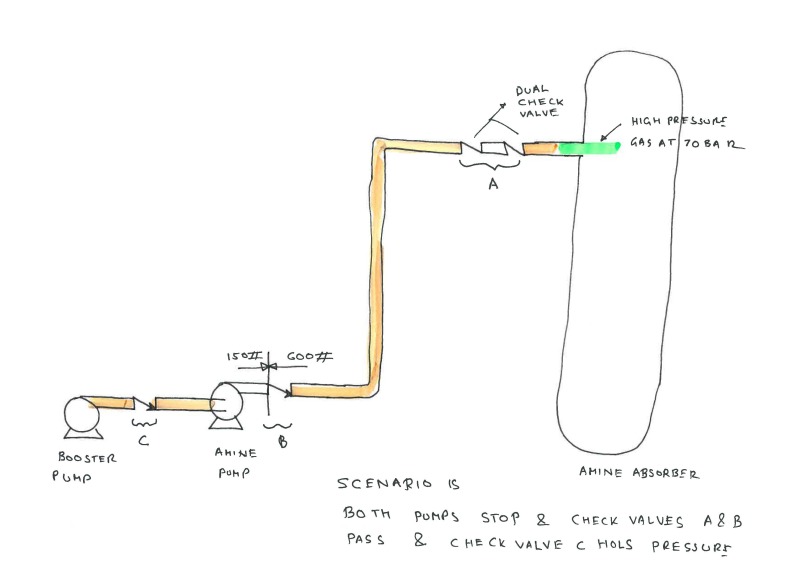