KimWT
Structural
- Jul 15, 2003
- 71
Hello!
I have to lift 5 ton roof precast concrete slab of elevator shaft to repair.
Isn't there any jackup tool to raise slab only 10" temporarily through 1/2" horizontal joint between this slab and elevator walls?
(Crane cannot access this area.)
This elevator shaft is located at the perimeter of parking structure and about 60ft tall;
two sides are attached to the parking deck.
I am looking for practical solution.
Thanks!
I have to lift 5 ton roof precast concrete slab of elevator shaft to repair.
Isn't there any jackup tool to raise slab only 10" temporarily through 1/2" horizontal joint between this slab and elevator walls?
(Crane cannot access this area.)
This elevator shaft is located at the perimeter of parking structure and about 60ft tall;
two sides are attached to the parking deck.
I am looking for practical solution.
Thanks!
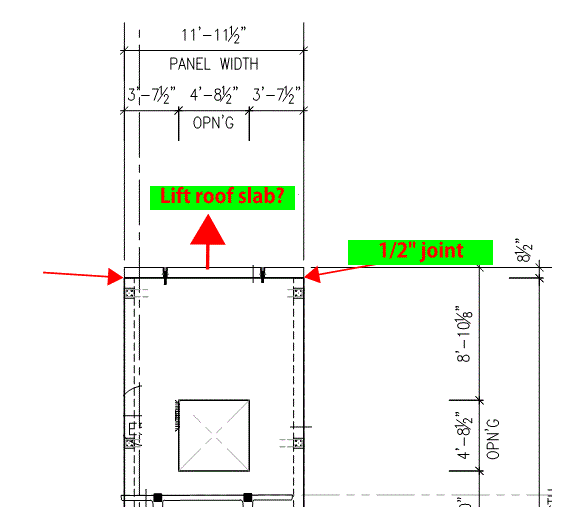