aehernan88
Mechanical
Hi, I am having a hard time understanding the true position for the Ø.199 holes in this drawing and how to measure them during inspection.
When the hole diameter is the smallest allowed or at MMC(.198) the center position of the hole can vary by Ø.002 from the true position. Is that correct?
What does the lower True Postion / .000 MMC block mean?
What's the best way to measure this using a Vision System?
What about using a functional gauge? Would the pins be Ø.197? What would be the position of the pins?
Thank you for the help!
When the hole diameter is the smallest allowed or at MMC(.198) the center position of the hole can vary by Ø.002 from the true position. Is that correct?
What does the lower True Postion / .000 MMC block mean?
What's the best way to measure this using a Vision System?
What about using a functional gauge? Would the pins be Ø.197? What would be the position of the pins?
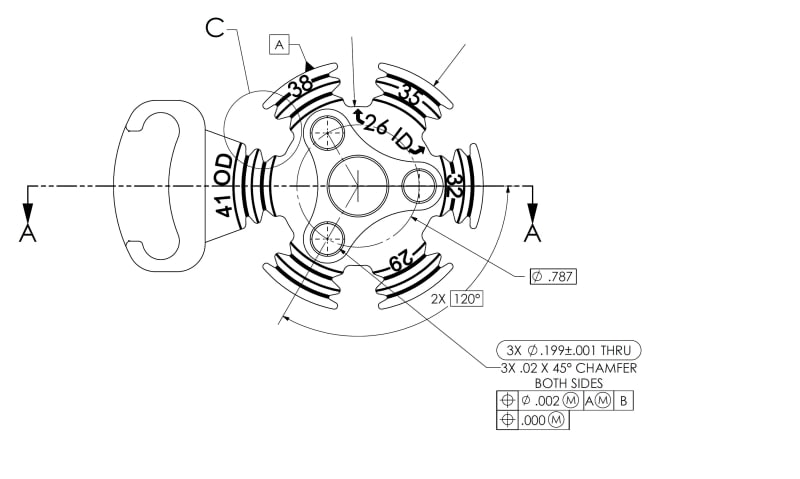
Thank you for the help!