Blackstar123
Civil/Environmental
- May 5, 2013
- 253
I've a structure supporting a steel silo.
I've calculated forces on the supporting beam assuming the load path as shown in attached Figures.
I'm trying to pass the supporting beams in torsion, which is coming out to be quite large due to heavy load (Tu = 130 KN-m = 1145 kip-in). There's a maximum limit beyond which I cannot increase the beam width further. This left me to play with the depth of beam and thicknesses only. Increasing depth is inadvertently increasing the eccentric moment due to horizontal force.
I'am thinking it's better to look at options to reduce the torsion first than keep on trying different beam sizes.
Question is, If a stiffener is provided at the junction of silo wall and hopper as shown in the figure below (which is not connected to supporting beam) then am I right in presuming that the horizontal force will not be transferred to the beam and it will be in equilibrium due to axial force in the stiffener?
P.S. I am not responsible for the design of steel silo. It is in the scope of others.
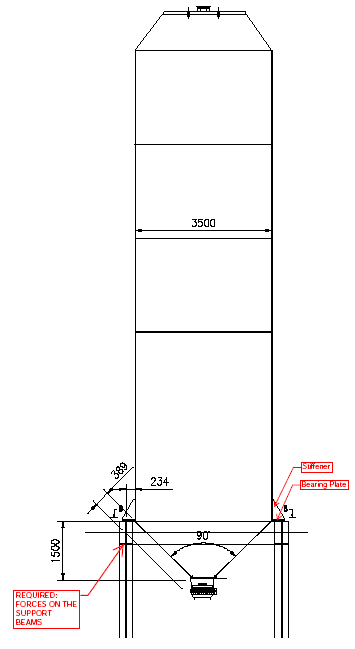
I've calculated forces on the supporting beam assuming the load path as shown in attached Figures.
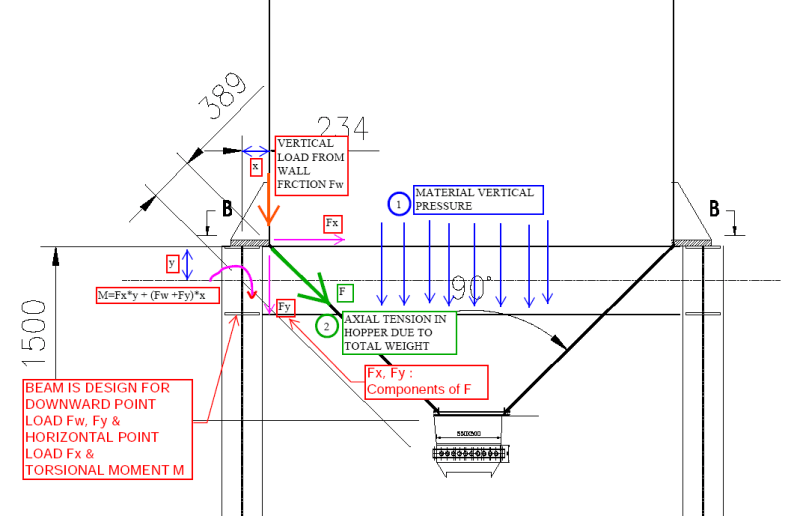
I'm trying to pass the supporting beams in torsion, which is coming out to be quite large due to heavy load (Tu = 130 KN-m = 1145 kip-in). There's a maximum limit beyond which I cannot increase the beam width further. This left me to play with the depth of beam and thicknesses only. Increasing depth is inadvertently increasing the eccentric moment due to horizontal force.
I'am thinking it's better to look at options to reduce the torsion first than keep on trying different beam sizes.
Question is, If a stiffener is provided at the junction of silo wall and hopper as shown in the figure below (which is not connected to supporting beam) then am I right in presuming that the horizontal force will not be transferred to the beam and it will be in equilibrium due to axial force in the stiffener?
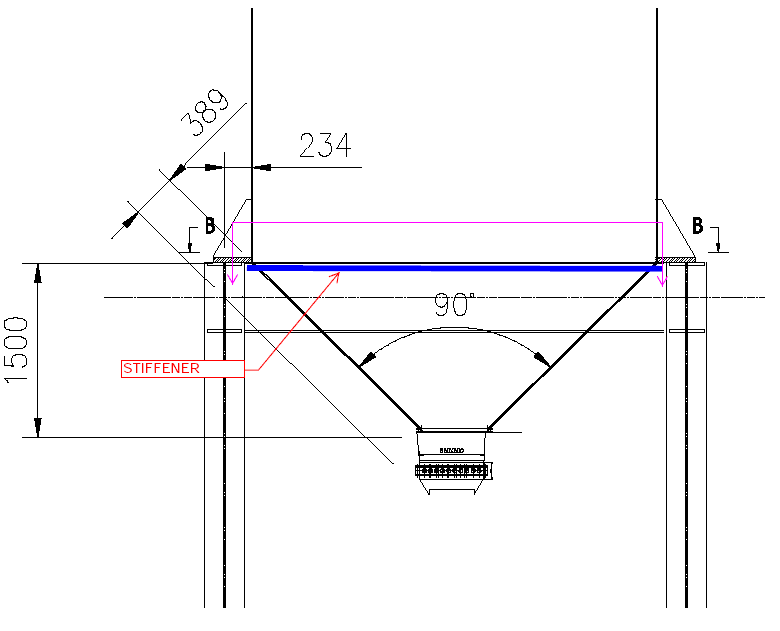
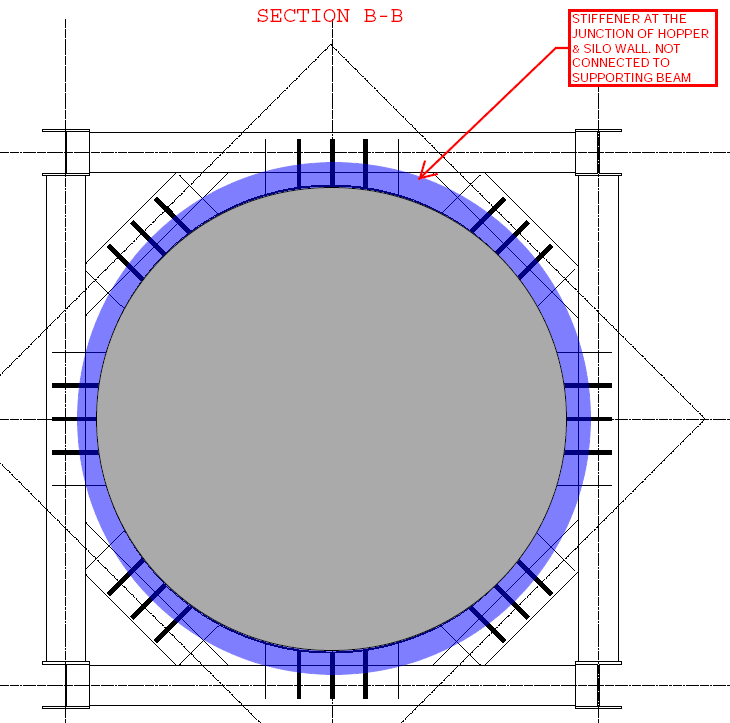
P.S. I am not responsible for the design of steel silo. It is in the scope of others.