PagoMitch
Mechanical
- Sep 18, 2003
- 71
I am helping a client commission some medium sized (34,000 CFM) chilled water AHU's that were installed several years ago, but never started. This is in a hospital, on an island with lots of rain and high humidity.
In cutting into a large (10 ft x 3ft) vertical SA plenum in order to get to some control dampers (long story), I discovered the duct interior is maybe 80% covered by what I believe is white rust.
It ...appears that the galvanized sheets were wet while being stored, corrosion occurred, and then they were cut up and formed and installed. In a few areas, iron oxide rust has started to form.
Note that in a hospital, internal duct lining/insulation is not allowed. Over time, internal lining breaks down, becomes friable, and (typically) black liner specs end up in the airstream, deposited on all horizontal spaces within the occupied space. Ironically, these AHUs and downstream ductwork were intended to replace the systems that had those exact issues.
Most of the sites I can find detailing solutions are aimed at cooling tower basins, inside heat exchangers, etc.
Anybody know the best/easiest/cheapest way to deal with this?
1. Ignore it? I would think it will only get worse, and then (I assume) start flaking off into the airstream. As this is in a hospital, that would not be a good thing.
2. Vinegar wash? I have seen this mentioned on several sites, but the acidic process is intended to REMOVE the zinc, then apply "neutralizing chemicals", which would then require re-galvanizing?
3. Wire brush and the apply an epoxy or spray galvanizing coating on top of the existing deteriorating surfaces?
4. Some other type of...PVC-based but Flame and smoke rated interior covering for the deteriorating galvanizing?
5. ???
TIA.
In cutting into a large (10 ft x 3ft) vertical SA plenum in order to get to some control dampers (long story), I discovered the duct interior is maybe 80% covered by what I believe is white rust.
It ...appears that the galvanized sheets were wet while being stored, corrosion occurred, and then they were cut up and formed and installed. In a few areas, iron oxide rust has started to form.
Note that in a hospital, internal duct lining/insulation is not allowed. Over time, internal lining breaks down, becomes friable, and (typically) black liner specs end up in the airstream, deposited on all horizontal spaces within the occupied space. Ironically, these AHUs and downstream ductwork were intended to replace the systems that had those exact issues.
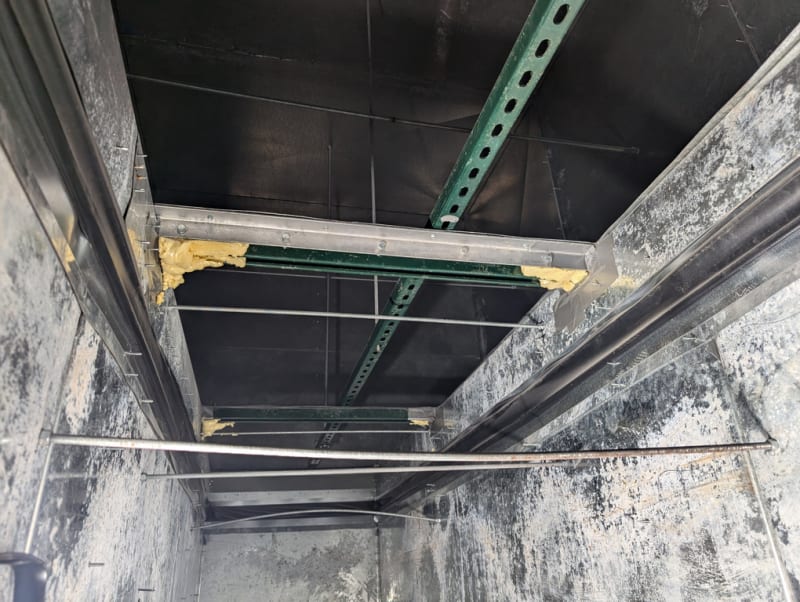
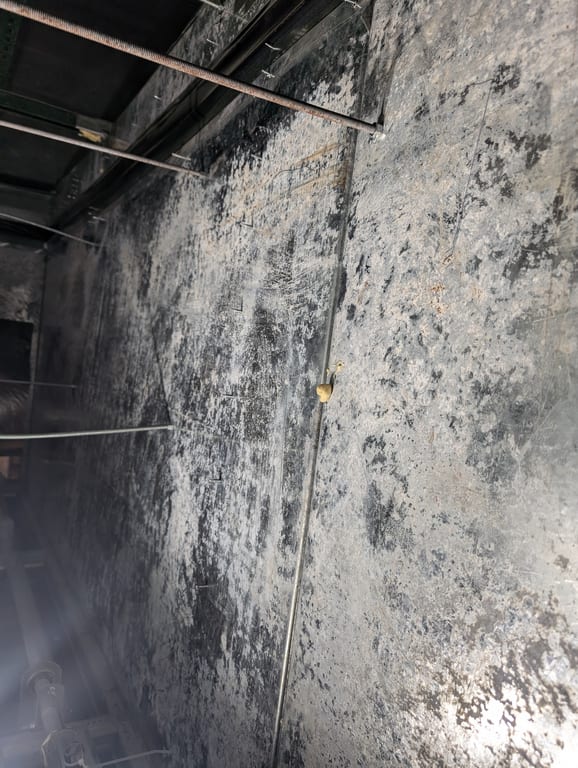
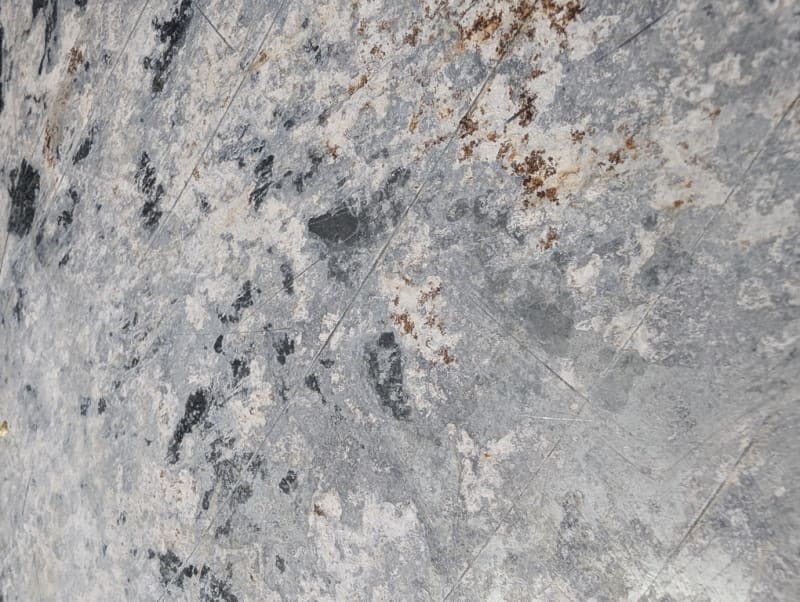
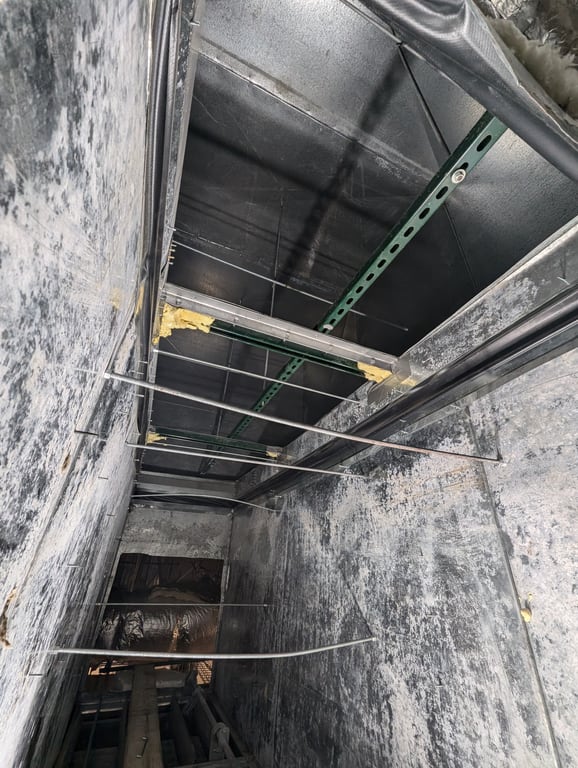
Most of the sites I can find detailing solutions are aimed at cooling tower basins, inside heat exchangers, etc.
Anybody know the best/easiest/cheapest way to deal with this?
1. Ignore it? I would think it will only get worse, and then (I assume) start flaking off into the airstream. As this is in a hospital, that would not be a good thing.
2. Vinegar wash? I have seen this mentioned on several sites, but the acidic process is intended to REMOVE the zinc, then apply "neutralizing chemicals", which would then require re-galvanizing?
3. Wire brush and the apply an epoxy or spray galvanizing coating on top of the existing deteriorating surfaces?
4. Some other type of...PVC-based but Flame and smoke rated interior covering for the deteriorating galvanizing?
5. ???
TIA.